Automobile hub spraying process
A technology for automobile wheels and crafts, applied in coatings, powder coatings, polyester coatings, etc., can solve problems such as rough surface of aluminum alloy wheels, corrosion damage of aluminum alloy wheels, weak adhesion of anti-corrosion coatings, etc., to overcome paint peeling Shedding, less demanding, improved chemical resistance
- Summary
- Abstract
- Description
- Claims
- Application Information
AI Technical Summary
Problems solved by technology
Method used
Examples
Embodiment 1
[0019] A kind of automobile hub spraying process is characterized in that comprising the following steps:
[0020] Step 1. Degrease, derust and polish the car hub, and the polishing includes sandblasting or grinding and polishing.
[0021] Step 2. Alkali etching treatment is carried out on the surface of the automobile wheel hub, and fluorocarbon spraying is carried out by electrostatic liquid phase spraying method to form a fluorocarbon coating. The fluorocarbon coating is synthesized with polyvinylidene fluoride resin as a base material and aluminum powder.
[0022] Carry out alkali etching treatment on the surface of the automobile hub, specifically including: preparing 50g / L alkali solution; adding 20g / L alkali etching agent to the alkali solution, and stirring evenly; after heating the alkali solution to 50°C, Submerge the aluminum alloy wheel hub into the alkaline solution; maintain the above temperature, and take out the aluminum alloy wheel hub after 5 minutes.
[002...
Embodiment 2
[0028] A kind of automobile hub spraying process is characterized in that comprising the following steps:
[0029] Step 1. Degrease, derust and polish the car hub, and the polishing includes sandblasting or grinding and polishing.
[0030] Step 2. Alkali etching treatment is carried out on the surface of the automobile wheel hub, and fluorocarbon spraying is carried out by electrostatic liquid phase spraying method to form a fluorocarbon coating. The fluorocarbon coating is synthesized with polyvinylidene fluoride resin as a base material and aluminum powder.
[0031] Carry out alkali etching treatment on the surface of the automobile hub, specifically including: preparing 50g / L alkali solution; adding 25g / L alkali etching agent to the alkali solution, and stirring evenly; after heating the alkali solution to 60°C, Submerge the aluminum alloy wheel hub into the alkaline solution; maintain the above temperature, and take out the aluminum alloy wheel hub after 8 minutes.
[003...
Embodiment 3
[0037] A kind of automobile hub spraying process is characterized in that comprising the following steps:
[0038] Step 1. Degrease, derust and polish the car hub, and the polishing includes sandblasting or grinding and polishing.
[0039] Step 2. Alkali etching treatment is carried out on the surface of the automobile wheel hub, and fluorocarbon spraying is carried out by electrostatic liquid phase spraying method to form a fluorocarbon coating. The fluorocarbon coating is synthesized with polyvinylidene fluoride resin as a base material and aluminum powder.
[0040] Carry out alkali etching treatment on the surface of the automobile hub, specifically including: preparing 65g / L alkali solution; adding 22g / L alkali etching agent to the alkali solution, and stirring evenly; after heating the alkali solution to 55°C, Submerge the aluminum alloy wheel hub into the alkaline solution; maintain the above temperature, and take out the aluminum alloy wheel hub after 6.5 minutes.
[0...
PUM
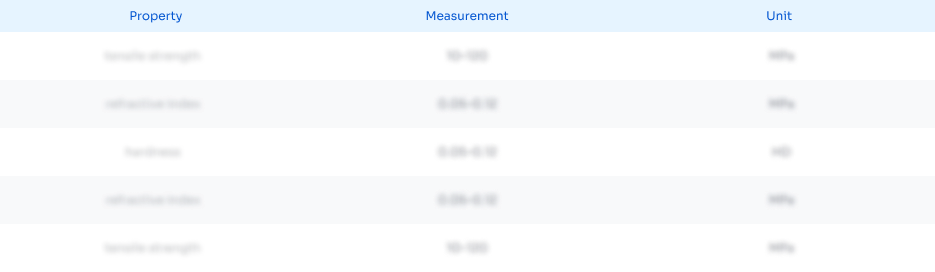
Abstract
Description
Claims
Application Information

- R&D
- Intellectual Property
- Life Sciences
- Materials
- Tech Scout
- Unparalleled Data Quality
- Higher Quality Content
- 60% Fewer Hallucinations
Browse by: Latest US Patents, China's latest patents, Technical Efficacy Thesaurus, Application Domain, Technology Topic, Popular Technical Reports.
© 2025 PatSnap. All rights reserved.Legal|Privacy policy|Modern Slavery Act Transparency Statement|Sitemap|About US| Contact US: help@patsnap.com