Production technology of polycarboxylate superplasticizer
A production process and technology of water reducing agent, applied in the field of production technology of polycarboxylate water reducing agent, can solve the problems of low water reducing rate, easy slump protection, strong temperature sensitivity, etc., achieve high water reducing rate and reduce carbonization The effect of depth, simple production process
- Summary
- Abstract
- Description
- Claims
- Application Information
AI Technical Summary
Problems solved by technology
Method used
Image
Examples
specific Embodiment 1
[0017] Specific embodiment 1. The production process steps of the polycarboxylate superplasticizer are: (1) Weigh the following components by weight ratio: 2500 parts of methallyl alcohol polyoxyethylene ether (VPEG-2400) (each part 1KG , the same below), 120 parts of acrylic acid, 450 parts of hydroxyethyl acrylate, 3 parts of vitamin C, 15 parts of 3-mercaptopropionic acid, 15 parts of hydrogen peroxide with a volume concentration of 27.5%, and 2750 parts of deionized water; Prepare material A, material B, material C, and material D in the following ways, of which material A is 2500 parts of methallyl alcohol polyoxyethylene ether (VPEG-2400), material B is composed of 120 parts of acrylic acid, 450 parts of hydroxyethyl acrylate, 280 parts of deionized water are uniformly mixed and dissolved in the batching tank. Material C is prepared by uniformly mixing and dissolving 3 parts of vitamin C, 15 parts of 3-mercaptopropionic acid, and 950 parts of deionized water in the batchi...
specific Embodiment 2
[0018] Specific Example 2: The production process steps of the polycarboxylate superplasticizer are: (1) Weigh the following components by weight ratio: 2600 parts of methallyl alcohol polyoxyethylene ether (VPEG-2400), 130 parts of acrylic acid , 500 parts of hydroxyethyl acrylate, 5 parts of vitamin C, 20 parts of 3-mercaptopropionic acid, 20 parts of hydrogen peroxide with a volume concentration of 27.5%, and 2950 parts of deionized water; the above-mentioned components are prepared in the following ways respectively A material, B Material, material C, material D, wherein material A is 2600 parts of methallyl alcohol polyoxyethylene ether (VPEG-2400), material B is made of 130 parts of acrylic acid, 500 parts of hydroxyethyl acrylate, and 300 parts of deionized water in the ingredients It is prepared by uniformly mixing and dissolving in the tank. Material C is prepared by uniformly mixing and dissolving 5 parts of vitamin C, 20 parts of 3-mercaptopropionic acid, and 1000 pa...
specific Embodiment 3
[0019]Specific Example Three: The production process steps of the polycarboxylate superplasticizer are: (1) Weigh the following components by weight ratio: 2800 parts of methallyl alcohol polyoxyethylene ether (VPEG-2400), 150 parts of acrylic acid , 550 parts of hydroxyethyl acrylate, 8 parts of vitamin C, 25 parts of 3-mercaptopropionic acid, 25 parts of hydrogen peroxide with a volume concentration of 27.5%, and 3,440 parts of deionized water; the above-mentioned components were prepared in the following ways A material, B Material, C material, D material, among which A material methallyl alcohol polyoxyethylene ether (VPEG-2400) 2800 parts, B material is composed of 150 parts of acrylic acid, 550 parts of hydroxyethyl acrylate, 360 parts of deionized water in the batching tank It is prepared by uniformly mixing and dissolving in the medium. Material C is prepared by uniformly mixing and dissolving 8 parts of vitamin C, 25 parts of 3-mercaptopropionic acid, and 1100 parts of...
PUM
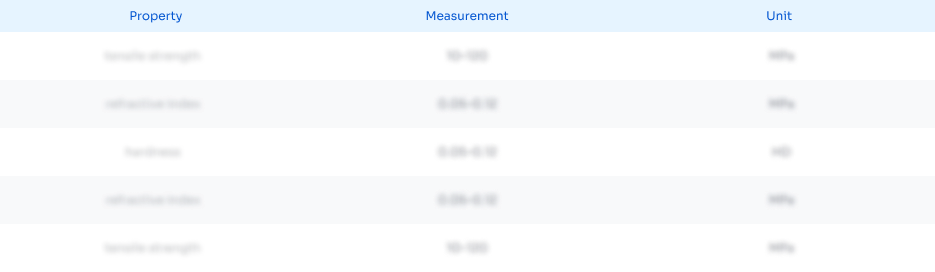
Abstract
Description
Claims
Application Information

- Generate Ideas
- Intellectual Property
- Life Sciences
- Materials
- Tech Scout
- Unparalleled Data Quality
- Higher Quality Content
- 60% Fewer Hallucinations
Browse by: Latest US Patents, China's latest patents, Technical Efficacy Thesaurus, Application Domain, Technology Topic, Popular Technical Reports.
© 2025 PatSnap. All rights reserved.Legal|Privacy policy|Modern Slavery Act Transparency Statement|Sitemap|About US| Contact US: help@patsnap.com