Comprehensive purification process of glass kiln smoke
A glass kiln and purification process technology, applied in the field of flue gas treatment, can solve the problem that the flue gas temperature cannot meet the requirements of denitration catalyst activity, and achieve the effect of ensuring long-term efficient and stable operation, no influence of kiln pressure, and high dust removal efficiency
- Summary
- Abstract
- Description
- Claims
- Application Information
AI Technical Summary
Problems solved by technology
Method used
Image
Examples
Embodiment Construction
[0020] The technical solutions of the present invention will be further described below in conjunction with the accompanying drawings and specific embodiments.
[0021] like figure 1 As shown, the equipment used in the glass kiln flue gas comprehensive purification process of the present invention includes a high-temperature electrostatic precipitator system, an SCR denitrification system and a semi-dry desulfurization system. SCR denitrification system includes SCR reactor, soot blowing system, metering cabinet, compressed air machine and chlorine water storage tank connected to the metering cabinet, and the output end of the metering cabinet is connected to a high-temperature electric dust collector; semi-dry The desulfurization system includes a desulfurization tower, a bag filter, and the desulfurization tower is connected with a slaked lime silo and a process water tank.
[0022] The concrete flow process of glass kiln flue gas comprehensive purification process of the p...
PUM
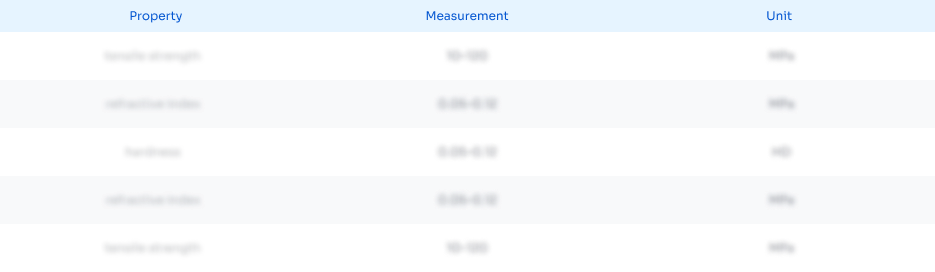
Abstract
Description
Claims
Application Information

- R&D
- Intellectual Property
- Life Sciences
- Materials
- Tech Scout
- Unparalleled Data Quality
- Higher Quality Content
- 60% Fewer Hallucinations
Browse by: Latest US Patents, China's latest patents, Technical Efficacy Thesaurus, Application Domain, Technology Topic, Popular Technical Reports.
© 2025 PatSnap. All rights reserved.Legal|Privacy policy|Modern Slavery Act Transparency Statement|Sitemap|About US| Contact US: help@patsnap.com