Milling cutter provided with equidistant arc head on eccentric shape flank surface and grinding method
A flank and arc head technology, which is applied to milling cutters, milling machine equipment, and tools for milling machines, etc., can solve the problems of cutting edge damage, small step distance, and low efficiency, so as to prolong tool life and improve tool quality. Life and the effect of reducing tool wear
- Summary
- Abstract
- Description
- Claims
- Application Information
AI Technical Summary
Problems solved by technology
Method used
Image
Examples
specific Embodiment approach 1
[0031] Specific implementation mode one: combine figure 1 , 2 , 4. An eccentric flank with unequal arc head milling cutter and grinding method, the cutter is of integral structure, and the cutter material is cemented carbide. The milling cutter includes a shank (1) and an arc head (2), the diameter of the shank is 8mm, the arc head includes a small curvature arc (2-2), the arc radius is 5mm, and a large curvature arc (2- 1), the arc radius is 1mm. The arcs at both ends are smoothly connected to form the arc head of the milling cutter. Effect: under the same pitch, increase the cutting bandwidth (d 2 >d 1 ), improved processing efficiency and improved processing quality (Δh 2 1 ).
specific Embodiment approach 2
[0032] Specific implementation mode two: combination figure 1 , 3 An eccentric flank with unequal distance arc head milling cutter and its grinding method, the included angle between (A-A) is 87°, the included angle between (B-B) is 93°, the helix angle (r) is 38°, and the helix angle (v) is 40°. Effect: It avoids the impact of different hardness of hardened steel splicing molds on the machining stability during the cutting process, reduces the tool vibration during the cutting process, and improves the tool life and the surface quality of the processed workpiece.
specific Embodiment approach 3
[0033] Specific implementation mode three: combination Figure 6 , 7 Disclosed is a milling cutter with an eccentric flank and an arc head with unequal distances and a grinding method thereof, wherein the end flank (6) and the peripheral flank (10) of the cutter are eccentric. Effect: It can protect the cutting edge, reduce tool wear and prolong tool life.
PUM
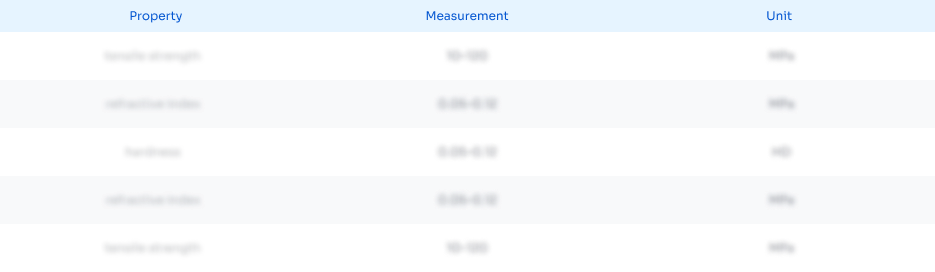
Abstract
Description
Claims
Application Information

- R&D Engineer
- R&D Manager
- IP Professional
- Industry Leading Data Capabilities
- Powerful AI technology
- Patent DNA Extraction
Browse by: Latest US Patents, China's latest patents, Technical Efficacy Thesaurus, Application Domain, Technology Topic, Popular Technical Reports.
© 2024 PatSnap. All rights reserved.Legal|Privacy policy|Modern Slavery Act Transparency Statement|Sitemap|About US| Contact US: help@patsnap.com