Preparation process of modern track low-floor motor train large-scale integral forging axle
A technology of integral forging and preparation process, applied in railway car body parts, vehicle parts, metal processing equipment, etc., can solve the problems of shrinkage, difficulty in ensuring process stability, etc., to reduce waste, improve yield, and ensure forging quality effect
- Summary
- Abstract
- Description
- Claims
- Application Information
AI Technical Summary
Problems solved by technology
Method used
Image
Examples
Embodiment 1
[0033] 1. Raw material preparation
[0034] Using low-alloy high-strength steel 34CrNiMo6 as raw material, the steel ingot is obtained by electric arc furnace melting and vacuum smelting, and then the low-alloy high-strength steel 34CrNiMo6 billet with a specification of Ф365mm×1100mm is obtained through electroslag remelting; among them, the composition of the low-alloy high-strength steel 34CrNiMo6 billet It is: the mass fraction of C element in the low-alloy high-strength steel 34CrNiMo6 billet is 0.30%, the mass fraction of Si is 0.40%, the mass fraction of Mn is 0.80%, the mass fraction of Cr is 1.30%, and the mass fraction of Mo is 0.30% , the mass fraction of Ni is 1.30%; the mass fraction of the P element in the low-alloy high-strength steel 34CrNiMo6 blank is 0.025%, and the mass fraction of the S element is 0.013%;
[0035] 2. Blank pre-forging
[0036] Use a three-ton free forging hammer to pull the blank into a pre-forged blank with three parts: the shaft head 1, ...
Embodiment 2
[0047] 1. Raw material preparation
[0048] Using low-alloy high-strength steel 34CrNiMo6 as raw material, the steel ingot is obtained by electric arc furnace melting and vacuum smelting, and then the low-alloy high-strength steel 34CrNiMo6 blank with a specification of Ф400mm)×1400mm is obtained through electroslag remelting. Among them, the low-alloy high-strength steel 34CrNiMo6 blank is The composition is: the mass fraction of C element in the low-alloy high-strength steel 34CrNiMo6 billet is 0.38%, the mass fraction of Si is 0.38%, the mass fraction of Mn is 0.50%, the mass fraction of Cr is 1.70%, and the mass fraction of Mo is 0.15% %, the mass fraction of Ni is 1.70%; the mass fraction of the P element in the low-alloy high-strength steel 34CrNiMo6 blank is 0.022%, and the mass fraction of the S element is 0.015%;
[0049] 2. Blank pre-forging
[0050] Use a three-ton free forging hammer to pull the blank into a pre-forged blank with three parts: the shaft head, the s...
Embodiment 3
[0061] 1. Raw material preparation
[0062] Using low-alloy high-strength steel 34CrNiMo6 as raw material, electric arc furnace melting and vacuum smelting are used to obtain steel ingots, and then electroslag remelting is used to obtain low-alloy high-strength steel 34CrNiMo6 blanks with a specification of Ф380mm×1200mm. Among them, the low-alloy high-strength steel 34CrNiMo6 blanks are The composition is: the mass fraction of C element is 0.33%, the mass fraction of Si is 0.35%, the mass fraction of Mn is 0.60%, the mass fraction of Cr is 1.40%, the mass fraction of Mo is 0.20%, and the mass fraction of Ni is 1.50 %; The mass fraction of the P element in the low-alloy high-strength steel 34CrNiMo6 blank is 0.023%, and the mass fraction of the S element is 0.014%;
[0063] 2. Blank pre-forging
[0064] Use a three-ton free forging hammer to pull the blank into a pre-forged blank with three parts: the shaft head, the shaft shoulder and the shaft waist (such as figure 1 shown...
PUM
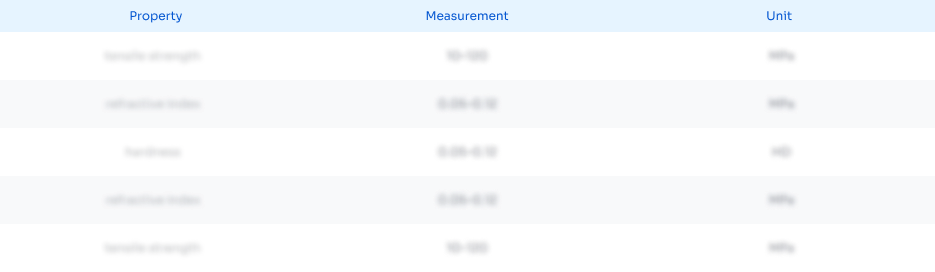
Abstract
Description
Claims
Application Information

- R&D Engineer
- R&D Manager
- IP Professional
- Industry Leading Data Capabilities
- Powerful AI technology
- Patent DNA Extraction
Browse by: Latest US Patents, China's latest patents, Technical Efficacy Thesaurus, Application Domain, Technology Topic, Popular Technical Reports.
© 2024 PatSnap. All rights reserved.Legal|Privacy policy|Modern Slavery Act Transparency Statement|Sitemap|About US| Contact US: help@patsnap.com