Method for converting limonite into magnetic iron mineral
A limonite and magnetic technology, applied in the field of comprehensive utilization of iron ore, can solve problems such as long roasting time, agglomeration, and unfavorable environment
- Summary
- Abstract
- Description
- Claims
- Application Information
AI Technical Summary
Problems solved by technology
Method used
Image
Examples
Embodiment 1
[0018] Referring to the attached picture, limonite ore with a TFe content of 32.8% and an S content of 2.06% is crushed by a jaw crusher to a particle size of less than 1.0mm, ground by a ball mill to -200, accounting for 60%-80%, and then pressed by a molding machine. For a small cylinder of 10mm×10mm, put the small cylinder into a magnetic field heat treatment device for magnetization roasting, the magnetic field strength is 0.93T, heat it to 850°C for 8-10 minutes, keep it warm for 5 minutes, and cool it by circulating water. After the sample cooled to room temperature, the sample was taken out. The magnetized and roasted sample was subjected to weak magnetic separation to obtain iron concentrate with a grade of 43% and an S content of 0.039%.
Embodiment 2
[0020] Referring to the attached picture, the limonite ore with a TFe content of 31.2% and a S content of 1.98% is crushed by a jaw crusher to a particle size of less than 1.0mm, ground by a ball mill to -200, accounting for 60%-80%, and then pressed by a molding machine. For a small cylinder of 10mm×10mm, put the small cylinder into a magnetic field heat treatment device for magnetization roasting, the magnetic field strength is 1T, heat it to 900°C for 8-10 minutes, keep it warm for 5 minutes, and cool it by circulating water. After the sample cooled to room temperature, the sample was taken out. The magnetized and roasted sample was subjected to weak magnetic separation to obtain iron concentrate with a grade of 48% and an S content of 0.043%.
Embodiment 3
[0022] Referring to the attached picture, limonite ore with a TFe content of 32.8% and an S content of 2.01% is crushed by a jaw crusher to a particle size of less than 1.0mm, ground by a ball mill to -200 to account for 60%-80%, and then pressed by a molding machine. For a small cylinder of 10mm×10mm, put the small cylinder into a magnetic field heat treatment device for magnetization roasting, the magnetic field strength is 1.5T, heat it to 950°C for 8-10 minutes, keep it warm for 5 minutes, and cool it by circulating water. After the sample cooled to room temperature, the sample was taken out. The magnetized and roasted sample was subjected to weak magnetic separation to obtain iron concentrate with a grade of 62% and an S content of 0.029%.
PUM
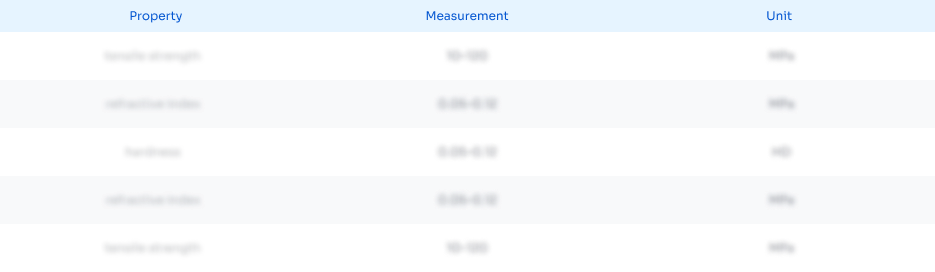
Abstract
Description
Claims
Application Information

- Generate Ideas
- Intellectual Property
- Life Sciences
- Materials
- Tech Scout
- Unparalleled Data Quality
- Higher Quality Content
- 60% Fewer Hallucinations
Browse by: Latest US Patents, China's latest patents, Technical Efficacy Thesaurus, Application Domain, Technology Topic, Popular Technical Reports.
© 2025 PatSnap. All rights reserved.Legal|Privacy policy|Modern Slavery Act Transparency Statement|Sitemap|About US| Contact US: help@patsnap.com