Heat-resistant electroplating solution
A technology of electroplating solution and heat resistance, applied in the field of electroplating solution, can solve the problems of corrosion configuration cost, poor heat resistance performance of electroplating solution, clean and clean, etc., and achieve the effect of low configuration cost, no corrosion and low corrosion.
- Summary
- Abstract
- Description
- Claims
- Application Information
AI Technical Summary
Problems solved by technology
Method used
Examples
Embodiment 1
[0009] A heat-resistant electroplating solution described in Example 1 is made up of the raw material components of the following parts: 50 parts of ammonium molybdate, 40 parts of ferrous ammonium sulfate, 35 parts of antimony potassium tartrate, 10 parts of protochloride Tin, 10 parts thioglycolic acid, 5 parts silver thiosulfate, 5 parts calcium thiosulfate, 5 parts aluminum sulfate, 5 parts sodium hexametaphosphate.
Embodiment 2
[0011] A heat-resistant electroplating solution described in Example 2 is made up of the raw material components of the following parts: 60 parts of ammonium molybdate, 45 parts of ferrous ammonium sulfate, 45 parts of antimony potassium tartrate, 15 parts of protochloride Tin, 15 parts thioglycolic acid, 10 parts silver thiosulfate, 8 parts calcium thiosulfate, 6 parts aluminum sulfate, 8 parts sodium hexametaphosphate.
PUM
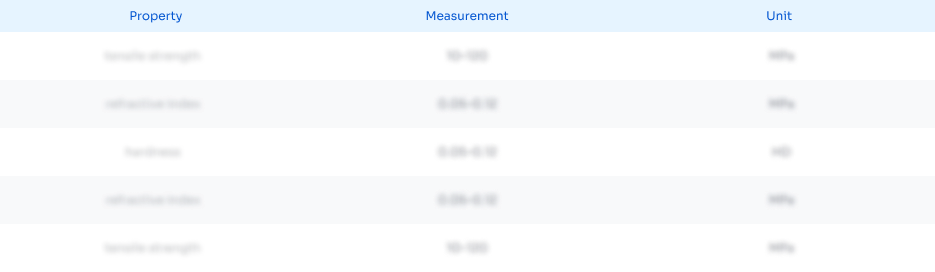
Abstract
Description
Claims
Application Information

- R&D
- Intellectual Property
- Life Sciences
- Materials
- Tech Scout
- Unparalleled Data Quality
- Higher Quality Content
- 60% Fewer Hallucinations
Browse by: Latest US Patents, China's latest patents, Technical Efficacy Thesaurus, Application Domain, Technology Topic, Popular Technical Reports.
© 2025 PatSnap. All rights reserved.Legal|Privacy policy|Modern Slavery Act Transparency Statement|Sitemap|About US| Contact US: help@patsnap.com