A method for realizing electroless plating antenna with a plastic shell embedded with metal
A technology for plastic shells and metal parts, applied in liquid chemical plating, metal material coating process, electrophoretic plating, etc. Strength, the effect of enhancing the user experience
- Summary
- Abstract
- Description
- Claims
- Application Information
AI Technical Summary
Problems solved by technology
Method used
Image
Examples
Embodiment Construction
[0040] The present invention will be described in detail below in conjunction with the drawings and embodiments.
[0041] See figure 1 , figure 1 It is a schematic flowchart of the first embodiment of the method provided by the present invention. The method includes:
[0042] Step 101: Perform the first electrophoretic coating on the metal parts;
[0043] Among them, the metal part may be a metal part formed by combining any metal or at least two metals in an alloy or non-alloy form.
[0044] Electrophoresis technology is a technology in which electrophoretic paint (or electrophoretic paint solution) is electrolyzed into charged paint ions under the action of both anode and cathode and applied voltage, and moves toward the electrode opposite to its electrical property, and finally deposits as an electrophoretic paint film. It includes an anodic electrophoresis process and a cathodic electrophoresis process. The objects to be coated are used as anode and cathode respectively, and nega...
PUM
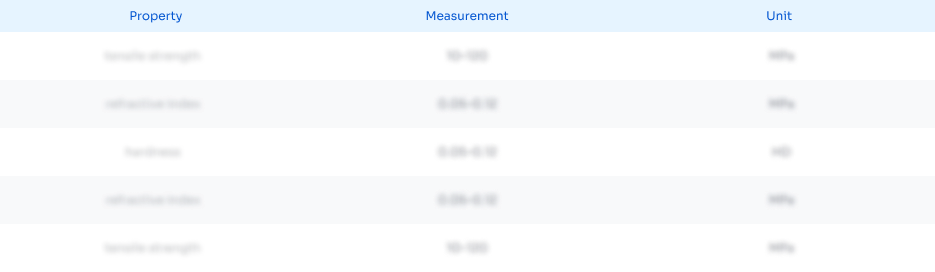
Abstract
Description
Claims
Application Information

- R&D
- Intellectual Property
- Life Sciences
- Materials
- Tech Scout
- Unparalleled Data Quality
- Higher Quality Content
- 60% Fewer Hallucinations
Browse by: Latest US Patents, China's latest patents, Technical Efficacy Thesaurus, Application Domain, Technology Topic, Popular Technical Reports.
© 2025 PatSnap. All rights reserved.Legal|Privacy policy|Modern Slavery Act Transparency Statement|Sitemap|About US| Contact US: help@patsnap.com