Sintering waste heat power generating system based on boosting power circuit
A technology of step-up power supply and waste heat power generation, which is applied in waste heat treatment, energy industry, machine/engine, etc. It can solve the problems of unstable operation of waste heat power generation, low utilization rate of thermal display, high operating cost, etc., so as to improve the scope of application and The effect of using range, reducing equipment investment, reducing equipment investment and operating cost
- Summary
- Abstract
- Description
- Claims
- Application Information
AI Technical Summary
Problems solved by technology
Method used
Image
Examples
Embodiment
[0025] Such as figure 1 As shown, the present invention includes a sintering machine hot flue gas system, a hot waste gas waste heat utilization system and a sintering waste heat power generation thermal system;
[0026] The hot flue gas system of the sintering machine is as follows: a hot flue gas outlet pipe 2 is provided in each of the bellows at the bottom of the sintering machine 1, and the other end of the hot flue gas outlet pipe 2 communicates with the hot flue gas manifold 26 at the tail. Each hot flue gas outlet pipe 2 is provided with a hot flue gas outlet pipe valve 27 at one end close to the hot flue gas manifold 26 at the tail, and a main exhaust fan 4 is arranged at one end of the hot flue gas manifold 26 at the tail, counting down from the tail of the sintering machine Starting from the second hot flue gas outlet pipe 2, hot flue gas branch pipes 28 and hot flue gas branch pipe valves 29 are arranged on 2 to 4 hot flue gas outlet pipes 2. The other end of the h...
PUM
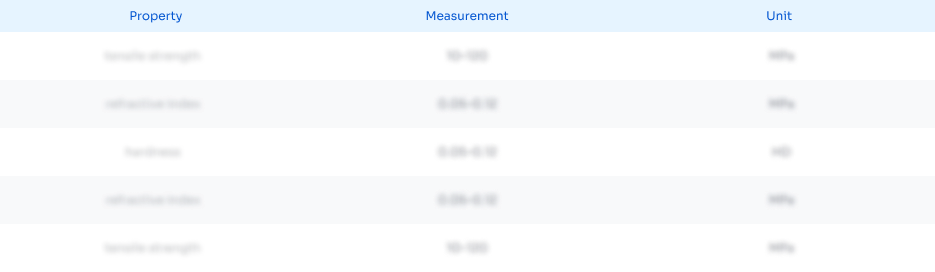
Abstract
Description
Claims
Application Information

- R&D
- Intellectual Property
- Life Sciences
- Materials
- Tech Scout
- Unparalleled Data Quality
- Higher Quality Content
- 60% Fewer Hallucinations
Browse by: Latest US Patents, China's latest patents, Technical Efficacy Thesaurus, Application Domain, Technology Topic, Popular Technical Reports.
© 2025 PatSnap. All rights reserved.Legal|Privacy policy|Modern Slavery Act Transparency Statement|Sitemap|About US| Contact US: help@patsnap.com