Heat preservation technology for continuous dip bleaching stage of one bath one step method for cotton fabric and cotton blended fabric
A technology of blended fabrics and footwork, which is applied in the continuous processing of textile materials, the processing of textile materials, textiles and papermaking, etc., can solve the problems of low fiber damage, heavy labor, and large body size, and achieve low fiber damage. Improve the efficiency of bleaching and enhance the effect of relaxation
- Summary
- Abstract
- Description
- Claims
- Application Information
AI Technical Summary
Problems solved by technology
Method used
Image
Examples
Embodiment Construction
[0068] The present invention will be described in detail below in conjunction with the accompanying drawings.
[0069] Such as figure 1 As shown, the one-bath one-step continuous soaking and bleaching stage heat preservation process of cotton and its blended fabrics of the present invention is characterized in that the main process flow includes the following steps in turn: cloth entry → first temperature zone heat preservation and bleaching step → second Temperature zone heat preservation and bleaching step→first washing step→second washing step→third washing step→pickling step→stacking step→squeezing step→fourth washing step→fifth washing step→sixth washing step→ Falling cloth; of which:
[0070] The above-mentioned step of heat preservation and bleaching in the first temperature zone, step of heat preservation and bleaching in the second temperature zone, first water washing step, second water washing step, third water washing step, stacking step, rolling water step, de-pi...
PUM
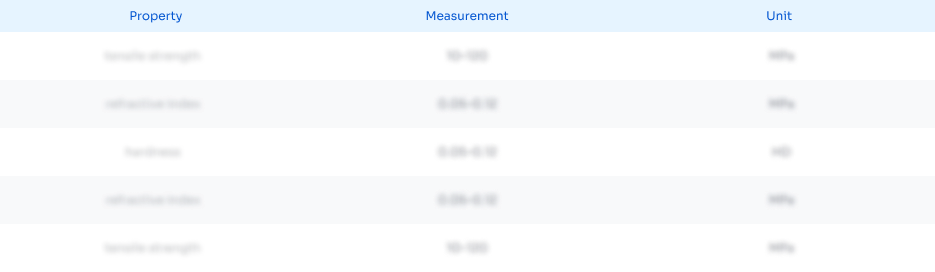
Abstract
Description
Claims
Application Information

- R&D
- Intellectual Property
- Life Sciences
- Materials
- Tech Scout
- Unparalleled Data Quality
- Higher Quality Content
- 60% Fewer Hallucinations
Browse by: Latest US Patents, China's latest patents, Technical Efficacy Thesaurus, Application Domain, Technology Topic, Popular Technical Reports.
© 2025 PatSnap. All rights reserved.Legal|Privacy policy|Modern Slavery Act Transparency Statement|Sitemap|About US| Contact US: help@patsnap.com