Power supply printed circuit board and processing method thereof
A technology for printed circuit boards and processing methods, applied in the directions of printed circuits, printed circuits, printed circuit manufacturing, etc., can solve the problems of large thickness and inconvenience, poor voltage withstand capability of power printed circuit boards, etc., to achieve convenient assembly, Satisfy the effect of high voltage resistance and improve the withstand voltage capability
- Summary
- Abstract
- Description
- Claims
- Application Information
AI Technical Summary
Problems solved by technology
Method used
Image
Examples
Embodiment Construction
[0028] In order to make the object, technical solution and advantages of the present invention clearer, the present invention will be further described in detail below in conjunction with the accompanying drawings and embodiments. It should be understood that the specific embodiments described here are only used to explain the present invention, not to limit the present invention.
[0029] Please refer to Figure 1 to Figure 3 , the processing method of the power supply printed circuit board provided by the embodiment of the present invention comprises the following steps:
[0030] S1: Provide a flexible copper-clad laminate 10 as an inner core board, the flexible copper-clad laminate 10 includes a polyimide substrate 11 and copper foil layers 12 disposed on two opposite surfaces of the polyimide substrate 11, The copper foil layer 12 is a rolled copper foil, and the copper foil layer 12 is processed by internal pattern transfer to form an internal circuit pattern (not shown)...
PUM
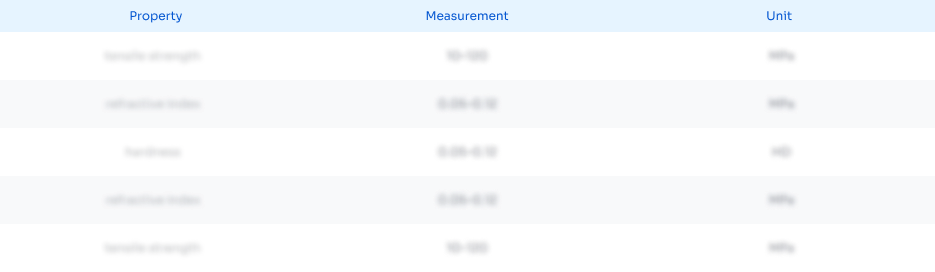
Abstract
Description
Claims
Application Information

- R&D Engineer
- R&D Manager
- IP Professional
- Industry Leading Data Capabilities
- Powerful AI technology
- Patent DNA Extraction
Browse by: Latest US Patents, China's latest patents, Technical Efficacy Thesaurus, Application Domain, Technology Topic, Popular Technical Reports.
© 2024 PatSnap. All rights reserved.Legal|Privacy policy|Modern Slavery Act Transparency Statement|Sitemap|About US| Contact US: help@patsnap.com