Silicone rubber microporous foam material adopting mixed cellular structure and preparation method of silicone rubber microporous foam material
A foam material and silicone rubber technology, which is applied in the field of silicone rubber microcellular foam materials of mixed cell structure and their preparation, can solve the problem of poor tensile strength of silicone rubber foam materials, complicated intermediate processes, and high dosage of pore-forming agents. problems, to achieve the effects of excellent comprehensive performance, high production efficiency and convenient control
- Summary
- Abstract
- Description
- Claims
- Application Information
AI Technical Summary
Problems solved by technology
Method used
Image
Examples
Embodiment 1
[0042] Step 1. Take 20 g of methyl vinyl silicone rubber with a vinyl content of 0.05 mol%, add it to a two-roll mill, and masticate it at room temperature for 5 minutes, then add 8.75 g of fumed silica and 0.5 mL of hydroxy silicone oil, Mix for 5 minutes, add 25g of urea, 1g of triallyl isocyanurate, continue mixing for 10 minutes to obtain a rubber compound, then store the rubber compound at room temperature for 24 hours, and then store it at room temperature Re-milling for 10 minutes, and then molding the rubber material that has been re-milled into a sheet or block on a tablet press; the rotating drum speed of the two-roll mill is set to 200r.min - 1 ; The die used in the molding is stainless steel;
[0043] Step 2. After the formed sheet or block is plastic-sealed, place it in the air at room temperature 60 The absorbed dose rate in the Coγ single-plate radiation field is 100Gy.min -1 Carry out radiation cross-linking at the position where the absorbed dose is 30kGy, ...
Embodiment 2
[0047] Step 1: Take 25g of methyl vinyl silicone rubber with a vinyl content of 0.1mol% and put it into a two-roll mill, masticate it at room temperature for 5 minutes, then add 3.8g of precipitated silica and 0.5mL of hydroxy silicone oil, Mix for 5 minutes, then add 20g urea, 1g triallyl cyanurate, continue mixing for 10 minutes to obtain a rubber compound, then store the rubber compound statically at room temperature for 24 hours, and then return to the compound at room temperature Refined for 10 minutes, then molded the finished compound into a sheet or block on a tablet press; the rotary drum speed of the two-roll mill was set at 300r.min -1 ; The die used in the molding is stainless steel;
[0048] Step 2. After the formed sheet or block is plastic-sealed, place it in the air at room temperature 60 Absorbed dose rate in Coγ single-plate radiation field is 107Gy.min -1 Carry out radiation cross-linking at the position where the absorbed dose is 45kGy, so that the rubber...
Embodiment 3
[0051] Step 1: Take 50g of methylvinyl silicone rubber with a vinyl content of 0.12mol% and put it into a two-roll mill, masticate it at room temperature for 5 minutes, then add 15g of precipitated silica, 1mL of hydroxy silicone oil, and knead 5 minutes, then add 35g urea, 2g trimethylolpropane trimethacrylate, continue to knead for 10 minutes, obtain sizing material, then said sizing material is statically stored at room temperature for 24 hours, and then returns to Refined for 10 minutes, then molded the finished compound into a sheet or block on a tablet press; the rotary drum speed of the two-roll mill was set at 400r.min -1 ; The die used in the molding is stainless steel;
[0052] Step 2. After the formed sheet or block is plastic-sealed, place it in the air at room temperature 60 The absorbed dose rate in the Coγ single-plate radiation field is 110Gy.min -1 Carry out radiation cross-linking at the position where the absorbed dose is 60kGy, so that the rubber can be c...
PUM
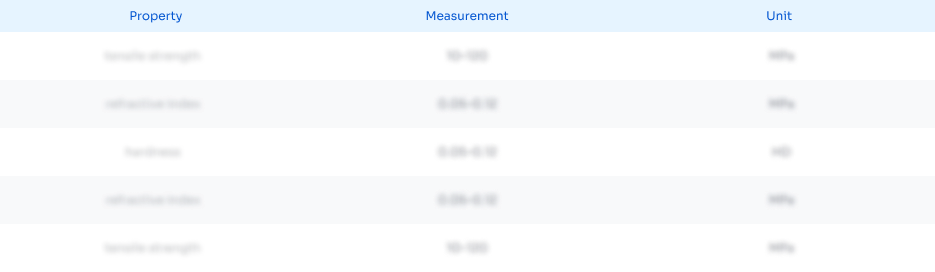
Abstract
Description
Claims
Application Information

- R&D
- Intellectual Property
- Life Sciences
- Materials
- Tech Scout
- Unparalleled Data Quality
- Higher Quality Content
- 60% Fewer Hallucinations
Browse by: Latest US Patents, China's latest patents, Technical Efficacy Thesaurus, Application Domain, Technology Topic, Popular Technical Reports.
© 2025 PatSnap. All rights reserved.Legal|Privacy policy|Modern Slavery Act Transparency Statement|Sitemap|About US| Contact US: help@patsnap.com