Disposal method for hot converter slag
A converter steel slag and disposal method technology, applied in recycling technology and other directions, can solve the problems of prolonging the cooling time, reducing the added value of cold steel slag for iron selection, and reducing the disposal efficiency, so as to reduce the content of free oxides and reduce the difficulty of subsequent disposal. , the effect of increasing the amount of recycling
- Summary
- Abstract
- Description
- Claims
- Application Information
AI Technical Summary
Problems solved by technology
Method used
Examples
Embodiment 1
[0019] Pour 1 ton of hot steel slag at 1550°C produced by the converter into the hot simmering pool, cover it, and pass CO 2 Cylinder will CO 2 Gas (at 25°C, CO 2 The volume content of the composition is 100%) into the heating pool, the inlet pipe is connected to a corner of the heating pool, and the exhaust pipe of the heating pool is arranged at a corner opposite to the heating pool (diagonal to the inlet). While the steel slag is being heated and stewed in water, the CO 2 The total gas flow rate is 20 cubic meters, the gas flow rate is 0.111 cubic meters per minute, the steel slag heating time is 3 hours, and the ventilation is stopped when the temperature of the hot steel slag drops to 25 °C. The test results show that the content of free calcium oxide in the steel slag after thermal stewing is 2.95%, and the recovery of metallic iron is increased by 1%.
Embodiment 2
[0021] Pour 150 tons of 1500°C hot steel slag produced by the converter into the hot simmering tank, cover it, and use the induced draft fan to blow the slag containing CO 2 Composition of exhaust gas (exhaust gas temperature is 200°C, CO 2 The volume content of the composition is 25%) into the hot stew pool, the inlet pipes are connected to the symmetrical four corners of the hot stew pool, and the exhaust pipe of the hot stew pool is arranged in the middle of the hot stew pool. While the steel slag is being heated and stewed in water, the designed waste gas intake is 1200 cubic meters in total, and the gas flow rate is 40 cubic meters per 0.5h; the rate of intake is 8 cubic meters. m / min, and the ventilation is completed within 10 minutes; the steel slag heating time is 15 hours, and the ventilation is stopped when the temperature of the hot slag drops to 200°C. The test results show that the content of free calcium oxide in the steel slag after thermal stewing is 2.0%, and...
Embodiment 3
[0023] Pour 30 tons of 1300°C hot steel slag produced by the converter into the unloadable pool, then transport the small pool to a cylindrical hollow container through the transportation equipment, seal it, and use the induced draft fan to drain the small pool containing CO 2 Composition of exhaust gas (exhaust gas temperature is 80°C, CO 2 The composition volume content is 52.8%) into the hollow container, the inlet pipe is connected to the middle of the bottom of the cylindrical equipment on one side, and the exhaust pipe is arranged on the other side of the middle of the cylindrical equipment. At the same time as the hot steel slag is soaked in water, the design waste gas intake is 900 cubic meters in total, the gas flow rate is 2.5 cubic meters per minute, the steel slag is simmered for 6 hours, and the hot slag temperature drops to 180 ° C. Stop ventilation. The test results show that the content of free calcium oxide in the steel slag after thermal stewing is 1.95%, an...
PUM
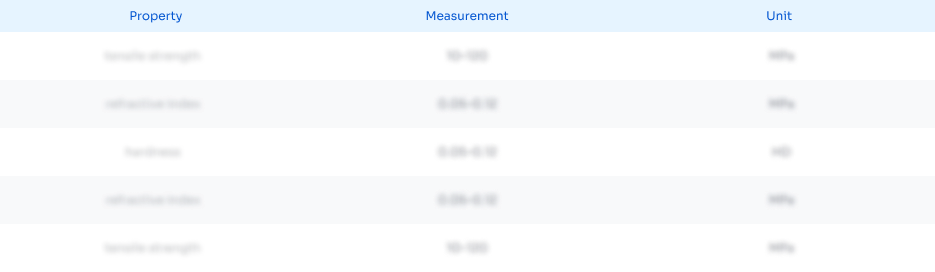
Abstract
Description
Claims
Application Information

- R&D
- Intellectual Property
- Life Sciences
- Materials
- Tech Scout
- Unparalleled Data Quality
- Higher Quality Content
- 60% Fewer Hallucinations
Browse by: Latest US Patents, China's latest patents, Technical Efficacy Thesaurus, Application Domain, Technology Topic, Popular Technical Reports.
© 2025 PatSnap. All rights reserved.Legal|Privacy policy|Modern Slavery Act Transparency Statement|Sitemap|About US| Contact US: help@patsnap.com