Ceramic microcrystal fused alumina grinding wheel for crankshaft grinding and manufacturing method thereof
A technology of ceramic crystallites and grinding wheels, which is applied in the manufacture of tools, abrasives, grinding devices, etc., can solve the problems of inability to process automobile crankshafts and high prices, and achieve a grinding wheel with good shape retention, low price and strong grinding ability. Effect
- Summary
- Abstract
- Description
- Claims
- Application Information
AI Technical Summary
Problems solved by technology
Method used
Image
Examples
Embodiment 1
[0054] Such as figure 1 , Shown in 2, the grinding wheel of the present invention includes a grinding part 1, a clamping part 2 and a grinding wheel hole 3, and the outer edge of the grinding part 1 has a Z-shaped interface.
[0055] The manufacturing steps of the present embodiment 1 are as follows:
[0056] 1) Selection of low-temperature vitrified bond agent No. 3 in Table 1: Weigh various raw materials, put them into a ball mill and mix for 18-20 hours, then melt, quench, pulverize, and sieve to make ceramic low-temperature bond.
[0057] 2) Ingredients:
[0058] a) Grinding part: weigh according to the grinding wheel formula, choose 80# for CA abrasive, choose 100# for ordinary corundum abrasive, 10 parts of ceramic microcrystalline corundum (CA) abrasive, 30 parts of single crystal corundum abrasive, 60 parts of white corundum abrasive, 18 parts of low temperature vitrified bond, 8 parts of pore former, 3 parts of whisker material, 4 parts of wetting agent, 1 part of c...
Embodiment 2
[0077] In the present embodiment, the grinding wheel structure is the same as that in Embodiment 1,
[0078] The manufacturing steps of this embodiment are as follows:
[0079] 1) Selection of low-temperature vitrified bond agent No. 4 scheme in Table 1: Weigh various raw materials, put them into a ball mill and mix for 18-20 hours, then melt, quench, pulverize, and sieve to make ceramic low-temperature bond.
[0080] 2) Ingredients:
[0081] a) Working layer: Weigh according to the grinding wheel formula, choose 60# for CA abrasive, choose 80# for ordinary corundum abrasive, 30 parts of ceramic microcrystalline corundum (CA) abrasive, 20 parts of single crystal corundum abrasive, 50 parts of white corundum abrasive, 15 Parts of low temperature vitrified binder, 5 parts of pore forming agent, 4 parts of whisker material, 3 parts of wetting agent, 0.9 part of coloring agent.
[0082] b) Non-working layer: weigh according to the grinding wheel formula, choose 80# corundum abra...
Embodiment 3
[0100] In the present embodiment, the grinding wheel structure is the same as that in Embodiment 1,
[0101] The manufacturing steps of this embodiment are as follows:
[0102] 1) Selection of low-temperature vitrified bond agent No. 5 scheme in Table 1: weigh various raw materials, put them into a ball mill and mix for 18-20 hours, then melt, quench, pulverize, and sieve to make ceramic low-temperature bond.
[0103] 2) Ingredients:
[0104] a) Working layer: weigh according to the grinding wheel formula, choose 70# for CA abrasive, choose 80# for ordinary corundum abrasive, 50 parts of ceramic microcrystalline corundum (CA) abrasive, 40 parts of single crystal corundum abrasive, 10 parts of white corundum abrasive, 20 Parts of low temperature ceramic bond, 10 parts of pore former, 2 parts of whisker material, 6 parts of wetting agent, 1.2 parts of coloring agent.
[0105] b) Non-working layer: weigh according to the formula of the grinding wheel, choose 80# corundum abrasi...
PUM
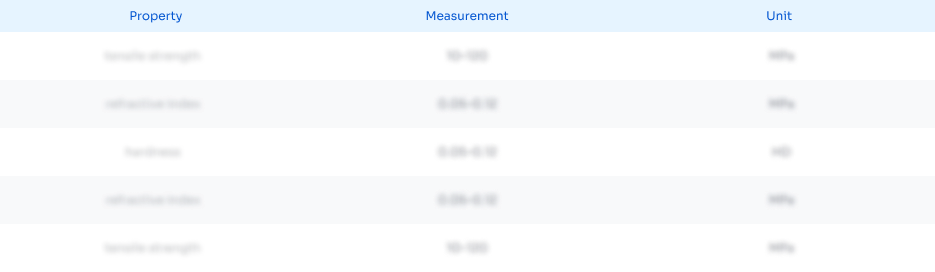
Abstract
Description
Claims
Application Information

- R&D
- Intellectual Property
- Life Sciences
- Materials
- Tech Scout
- Unparalleled Data Quality
- Higher Quality Content
- 60% Fewer Hallucinations
Browse by: Latest US Patents, China's latest patents, Technical Efficacy Thesaurus, Application Domain, Technology Topic, Popular Technical Reports.
© 2025 PatSnap. All rights reserved.Legal|Privacy policy|Modern Slavery Act Transparency Statement|Sitemap|About US| Contact US: help@patsnap.com