A Servo Motor Control Method Combining Sliding Mode Control and Fractional Neural Network Control
A neural network control and servo motor technology, applied in the control of generators, motor generator control, electronic commutation motor control, etc., can solve the problem that sliding mode control technology no longer has strong robustness, affects system tracking performance, and system Tremor and other issues
- Summary
- Abstract
- Description
- Claims
- Application Information
AI Technical Summary
Problems solved by technology
Method used
Image
Examples
Embodiment 1
[0115] In this embodiment, a permanent magnet synchronous motor is taken as an example to describe the implementation process of the present invention. The control method of the permanent magnet synchronous motor in this embodiment includes the following four steps:
[0116] (1) Describe the permanent magnet synchronous motor model
[0117] The mathematical model of the permanent magnet synchronous motor in the rotating coordinate system is:
[0118]
[0119] The corresponding electromagnetic torque equation is:
[0120]
[0121] The corresponding kinetic equation is:
[0122]
[0123] By applying vector control, the dynamic equation (3) can be simplified as:
[0124]
[0125] Substituting the dynamic equation (4) into the electromagnetic torque equation (2), we can get:
[0126]
[0127] Considering the change of motor parameters, the above formula can be expressed as:
[0128]
[0129] The purpose of controller design is to find a suitable control law so...
no. 2 example
[0183] The control method proposed by the invention has been successfully applied to the speed loop of the permanent magnet synchronous motor drive system. The structure of the speed loop of the permanent magnet synchronous motor drive system is composed of speed controller, coordinate transformation module, pulse width speed regulation module, inverter, permanent magnet synchronous motor (PMSM) and encoder and other modules, such as Figure 5 shown.
[0184] The speed loop controller is implemented on TI's dsp chip stm320f2812. The servo motor is a Japanese Sanyo permanent magnet synchronous motor (PMSM), with a power of 1kw and a rated speed of 1000r / min. The load disturbance outside the system is simulated by changing the load of the motor.
[0185] The specific algorithm and control flow of the speed loop of the permanent magnet synchronous motor drive system are as follows: Figure 6 and Figure 7 As shown, the sinusoidal tracking result of the speed loop of the permane...
PUM
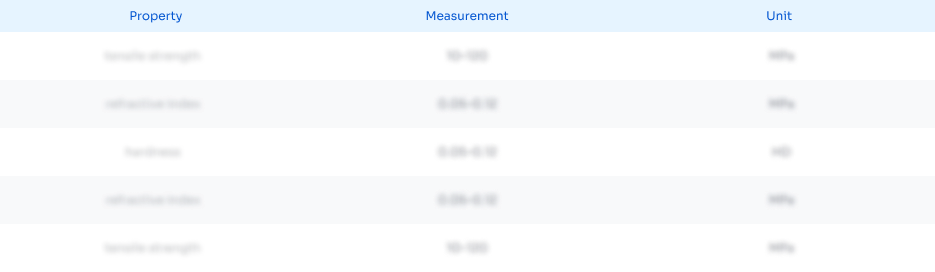
Abstract
Description
Claims
Application Information

- Generate Ideas
- Intellectual Property
- Life Sciences
- Materials
- Tech Scout
- Unparalleled Data Quality
- Higher Quality Content
- 60% Fewer Hallucinations
Browse by: Latest US Patents, China's latest patents, Technical Efficacy Thesaurus, Application Domain, Technology Topic, Popular Technical Reports.
© 2025 PatSnap. All rights reserved.Legal|Privacy policy|Modern Slavery Act Transparency Statement|Sitemap|About US| Contact US: help@patsnap.com