Ultra-thin high-coverage impregnated base paper and its preparation method
A high-coverage, ultra-thin technology, applied in papermaking, paper machines, textiles and papermaking, etc., can solve the problems of reducing base paper basis weight, poor base paper strength, easy paper breakage, and large base paper basis weight, so as to reduce raw material costs and reduce strength. Deformation, high output rate effect
- Summary
- Abstract
- Description
- Claims
- Application Information
AI Technical Summary
Problems solved by technology
Method used
Image
Examples
Embodiment 1
[0029]Embodiments 1 to 5 are specific embodiments of the ultra-thin high-coverage impregnated base paper of the present invention and its preparation method, wherein embodiment 1 is the best embodiment.
[0030] Table 1 The composition of the components of Examples 1 to 5 (by weight)
[0031]
[0032] Example 1
[0033] 1) Put the bleached coniferous pulp and bleached hardwood pulp into the pulper equipped with 36°C pulping water to fully disintegrate, and control the beating degree to 32°SR and 36°SR respectively, and the mass concentration reaches 4.5% Afterwards, it is pumped into the crushing tank for standby;
[0034] 2) Dilute the mineral filler with water to a mass concentration of 65%, add pigment, and then fully stir with a high-speed mixer at a speed of 3000 rpm to disperse the mineral filler and pigment evenly, and finally pump it into the crushing tank of step 1) Mix evenly with the product obtained in step 1) to obtain a mixed slurry;
[0035] 3) After the p...
Embodiment 2
[0038] 1) Put the bleached coniferous pulp and bleached hardwood pulp into the pulper equipped with 40°C pulping water to fully disintegrate, and control the degree of beating to 31°SR and 38°SR respectively, and the mass concentration reaches 4.5%. Afterwards, it is pumped into the crushing tank for standby;
[0039] 2) Dilute the mineral filler with water to a mass concentration of 70%, add pigment, and then fully stir with a high-speed mixer at a speed of 3000 rpm to disperse the mineral filler and pigment evenly, and finally pump it into the crushing tank of step 1) Mix evenly with the product obtained in step 1) to obtain a mixed slurry;
[0040] 3) After the pulp mixed in step 2) passes through the fiber disintegrator to defiberize the fiber, it is refined by a double disc mill beater to cut and separate the fiber; the refined pulp is poured into the filling tank for Add filling, add wet strength agent, retention aid and defoamer in proportion in turn, and finally adjus...
Embodiment 3
[0043] 1) Put the bleached coniferous pulp and bleached hardwood pulp into the pulper equipped with pulping water at 45°C to fully disintegrate, and control the degree of beating to 32°SR and 36°SR respectively, and the mass concentration reaches 4.5%. Afterwards, it is pumped into the crushing tank for standby;
[0044] 2) Dilute the mineral filler with water to a mass concentration of 75%, add pigment, and then fully stir with a high-speed mixer at a speed of 3000 rpm to disperse the mineral filler and pigment evenly, and finally pump it into the crushing tank of step 1) Mix evenly with the product obtained in step 1) to obtain a mixed slurry;
[0045] 3) After the pulp mixed in step 2) passes through the fiber disintegrator to defiberize the fiber, it is refined by a double disc mill beater to cut and separate the fiber; the refined pulp is poured into the filling tank for Add filling, add wet strength agent, retention aid and defoamer in proportion in turn, and finally ad...
PUM
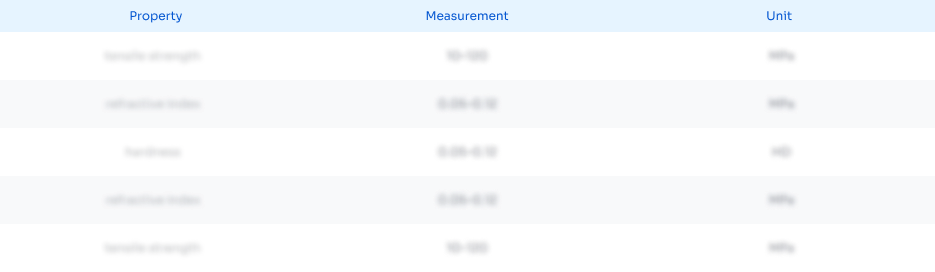
Abstract
Description
Claims
Application Information

- Generate Ideas
- Intellectual Property
- Life Sciences
- Materials
- Tech Scout
- Unparalleled Data Quality
- Higher Quality Content
- 60% Fewer Hallucinations
Browse by: Latest US Patents, China's latest patents, Technical Efficacy Thesaurus, Application Domain, Technology Topic, Popular Technical Reports.
© 2025 PatSnap. All rights reserved.Legal|Privacy policy|Modern Slavery Act Transparency Statement|Sitemap|About US| Contact US: help@patsnap.com