Method for preparing gradient thermal barrier coating
A thermal barrier coating, gradient technology, applied in the direction of coating, metal material coating process, fusion spray plating, etc., can solve the problems of many process influencing factors, no mature technical solution, and immature gradient thermal barrier coating method. , to achieve the effect of improving bonding force, improving wettability and alleviating thermal stress
- Summary
- Abstract
- Description
- Claims
- Application Information
AI Technical Summary
Problems solved by technology
Method used
Image
Examples
Embodiment 1
[0024] Preparation of ZrO on the Surface of Titanium Alloy TC4 2 Gradient thermal barrier coating, specifically as follows:
[0025] The first step is to soak the cut titanium alloy substrate in acetone for 5-8 minutes to remove oil stains, take the titanium alloy out of the acetone, wash it with clean water, dry it, and finally perform sandblasting treatment to strengthen the substrate and thermal barrier Coating contact area.
[0026] In the second step, the 25nm ZrO 2 Initial Nanoparticle Doping Micron-scale Y 2 o 3 powder, to obtain doped ceramic particles, Y 2 o 3 The mass of the powder accounts for 5% of the mass of the doped ceramic particles. The doped ceramic particles are prepared by spray drying to obtain micron-sized ceramic particles of 40-70 μm. The main process parameters of spray drying are drying air temperature 270 ° C, atomizer frequency 150 Hz, The speed of the feed pump is 30r / min, and the temperature of the air outlet is 110°C. Finally, the surface...
Embodiment 2
[0030] Preparation of Al on the surface of Q235 steel 2 o 3 Gradient thermal barrier coating, specifically as follows:
[0031] The first step is to soak the cut Q235 steel substrate in acetone for 5-8 minutes to remove oil stains, remove the titanium alloy from the acetone, wash it with clean water, dry it, and finally perform sandblasting treatment to strengthen the substrate and coating the contact area.
[0032] In the second step, 40nm Al 2 o 3 The initial nanoparticles are doped with micron-level CaO powder to obtain doped ceramic particles. The mass of CaO powder accounts for 7% of the mass of doped ceramic particles. The doped ceramic particles are prepared by spray drying to obtain micron-sized ceramic particles of 50-80 μm, which are spray-dried The main process parameters are drying air temperature 270°C, atomizer frequency 150Hz, feed pump speed 30r / min, air outlet temperature 110°C. Finally, the surface coating of the ceramic particles is carried out, and the...
Embodiment 3
[0036] Preparation of ZrO on the surface of Q235 steel 2 Gradient thermal barrier coating, specifically as follows:
[0037] In the first step, soak the cut Q235 steel substrate in acetone for 5-8 minutes to remove oil stains, take the Q235 steel out of the acetone, wash it with clean water, and dry it.
[0038] In the second step, 40nm ZrO 2 The initial nanoparticles are doped with micron-level MgO powder to obtain doped ceramic particles. The mass of MgO powder accounts for 8% of the mass of doped ceramic particles. The doped ceramic particles are prepared by spray drying to obtain micron-sized ceramic particles of 40-70 μm, which are spray-dried The main process parameters are drying air temperature 270°C, atomizer frequency 130Hz, feed pump speed 30r / min, air outlet temperature 110°C. Finally, the surface coating of the ceramic particles is carried out, and the nickel-based alloy powder is coated on the surface of the doped ceramic particles by means of electroless plati...
PUM
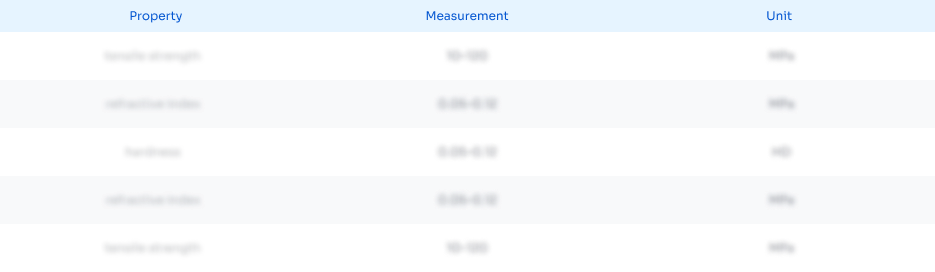
Abstract
Description
Claims
Application Information

- R&D Engineer
- R&D Manager
- IP Professional
- Industry Leading Data Capabilities
- Powerful AI technology
- Patent DNA Extraction
Browse by: Latest US Patents, China's latest patents, Technical Efficacy Thesaurus, Application Domain, Technology Topic, Popular Technical Reports.
© 2024 PatSnap. All rights reserved.Legal|Privacy policy|Modern Slavery Act Transparency Statement|Sitemap|About US| Contact US: help@patsnap.com