Preparation method of epoxy resin conductive adhesive for bonding LED chip
An LED chip and epoxy resin technology, applied in the field of conductive adhesive, can solve the problems of low adhesion of workpieces and easy to fall off, and achieve the effect of improving thermal conductivity, shear strength and electrical conductivity.
- Summary
- Abstract
- Description
- Claims
- Application Information
AI Technical Summary
Problems solved by technology
Method used
Image
Examples
preparation example Construction
[0029] The preparation method of the above-mentioned components can be uniformly mixed according to common methods, and then ground.
[0030] After the conductive adhesive is applied on the working surface, it can be cured by heating or curing at room temperature. It is preferably cured under the condition of heating to 80-90° C. for 4-6 hours.
Embodiment 1
[0032] Add 10g of monomer 3-methylcatechol, 4g of hydroxymalonic acid, 12g of m-trifluoromethylphenol and 15g of 4,4'-dihydroxybiphenyl into 90g of epichlorohydrin, mix well, and then add 30wt% NaOH aqueous solution, wherein the molar amount of NaOH is 0.8 times of the total hydroxyl groups in the four monomers, connect the condenser to reflux, stir and react at 60°C for 1 hour, then raise the temperature to 90°C, and react for 2 hours After finishing the reaction, evaporate the solvent to dryness, then dissolve the residue in methyl isobutyl ketone, wash with water, remove the water phase, and evaporate the solvent to dryness in the organic phase to obtain a modified epoxy resin.
[0033] The modified epoxy resin obtained is mixed with bisphenol A type epoxy resin 45g, poly-1,3-trimethylene glycol ester 10g (crystalline polyester resin), ethylene glycol glycidyl ether 12g (epoxy resin) Resin diluent), micron spherical silver powder 400g, tert-butylpyrogallol 4g (curing agent)...
Embodiment 2
[0035] Add 20g of monomer 3-methylcatechol, 6g of hydroxymalonic acid, 16g of m-trifluoromethylphenol and 30g of 4,4'-dihydroxybiphenyl into 140g of epichlorohydrin, mix well, and then add 30wt% NaOH aqueous solution, wherein the molar weight of NaOH is 1.2 times of the total hydroxyl groups in the four monomers, connect the condenser to reflux, stir and react at 60°C for 3 hours, then heat up to 90°C, and react for 4 hours After finishing the reaction, evaporate the solvent to dryness, then dissolve the residue in methyl isobutyl ketone, wash with water, remove the water phase, and evaporate the solvent to dryness in the organic phase to obtain a modified epoxy resin.
[0036] The modified epoxy resin obtained is mixed with bisphenol A type epoxy resin 60g, poly-1,3-trimethylene glycol ester 12g (crystalline polyester resin), ethylene glycol glycidyl ether 15g (epoxy resin) Resin diluent), micron spherical silver powder 700g, tert-butylpyrogallol 9g (curing agent), 2-ethyl 4-...
PUM
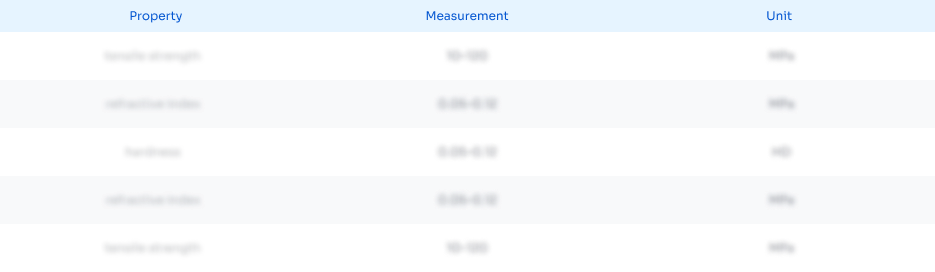
Abstract
Description
Claims
Application Information

- R&D Engineer
- R&D Manager
- IP Professional
- Industry Leading Data Capabilities
- Powerful AI technology
- Patent DNA Extraction
Browse by: Latest US Patents, China's latest patents, Technical Efficacy Thesaurus, Application Domain, Technology Topic, Popular Technical Reports.
© 2024 PatSnap. All rights reserved.Legal|Privacy policy|Modern Slavery Act Transparency Statement|Sitemap|About US| Contact US: help@patsnap.com