Basalt fiber manufacturing process
A technology of basalt fiber and manufacturing process, which is applied in the direction of manufacturing tools and glass manufacturing equipment, etc. It can solve the problems of mineral waste and unstable fiber processing quality, and achieve good mixing effect, good melt uniform effect, and guaranteed accuracy.
- Summary
- Abstract
- Description
- Claims
- Application Information
AI Technical Summary
Problems solved by technology
Method used
Image
Examples
Embodiment Construction
[0024] Such as figure 1 As shown, the basalt fiber manufacturing equipment includes a pool kiln 101, a heating electrode 103, an exhaust device 102, a monitoring rod 105, a drain plate 106, an injection device 107, and a cotton collecting pipe 108. An exhaust device 102 is installed on the kiln 101, and the feeding port 109 is arranged on the top of the kiln 101; the heating electrode 103 is arranged on the side walls around the bottom of the kiln 101, or can also be arranged in the kiln; the observation window 104 is arranged On the side wall of the tank kiln 101, the monitoring rod 105 is fixed inside the tank kiln 101, and its front end is fixed with a liquid level substrate 111; through the observation window 104, the operator can observe whether the liquid level of the melt coincides with the bottom surface of the liquid level substrate 111. The drain plate 106 is installed at the discharge port at the bottom of the tank kiln 101, and can be a platinum-rhodium drain plate...
PUM
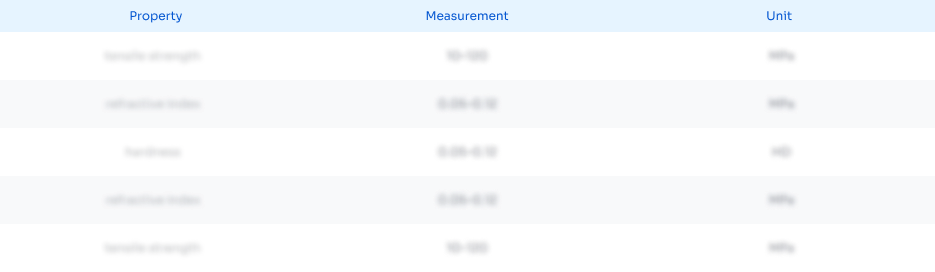
Abstract
Description
Claims
Application Information

- R&D
- Intellectual Property
- Life Sciences
- Materials
- Tech Scout
- Unparalleled Data Quality
- Higher Quality Content
- 60% Fewer Hallucinations
Browse by: Latest US Patents, China's latest patents, Technical Efficacy Thesaurus, Application Domain, Technology Topic, Popular Technical Reports.
© 2025 PatSnap. All rights reserved.Legal|Privacy policy|Modern Slavery Act Transparency Statement|Sitemap|About US| Contact US: help@patsnap.com