Method for producing zirconium tetrachloride
A production method, the technology of zirconium tetrachloride, is applied in the direction of zirconium halide, silicon halide compound, halosilane, etc., which can solve the problems of unfavorable energy saving, high replacement cost, and large power consumption, so as to reduce the maintenance time of shutdown, The effect of reducing production cost and improving production efficiency
- Summary
- Abstract
- Description
- Claims
- Application Information
AI Technical Summary
Problems solved by technology
Method used
Examples
specific Embodiment 1
[0032] Grind zircon sand to 325 mesh, petroleum coke powder to 200 mesh, and silicon carbide to 325 mesh, firstly mix zircon sand, petroleum coke powder and silicon carbide powder into the boiling chlorination furnace at the same time, and Chlorine gas is introduced to carry out the chlorination reaction. The weight ratio of zircon sand, petroleum coke powder and silicon carbide is 1:0.1:0.32. Keep the fluidized furnace temperature at 1100°C, the reaction formula of silicon carbide and chlorine gas is: SiC+2Cl2=SiCl4+C, the main reaction formula of producing zirconium tetrachloride by chlorination of zircon sand is: ZrSiO4+4C+4Cl2=ZrCl4+SiCl4 +4CO. The chlorinated products and by-products are discharged from the top of the fluidized chlorination furnace, and the slag is discharged from the lower part of the fluidized chlorination furnace. This process is a continuous operation process of continuous feeding and continuous discharging. Silicon carbide can be used in the product...
specific Embodiment 2
[0033]Crush zircon sand to 325 mesh, petroleum coke powder to 200 mesh, and metal silicon to 325 mesh. First, mix zircon sand, petroleum coke powder, and metal silicon powder into the boiling chlorination furnace at the same time, and pass through Chlorine gas is added to carry out the chlorination reaction. The feeding ratio of zircon sand, petroleum coke powder and metal silicon is: 1:0.25:0.36. Keep the fluidized furnace temperature at 1100°C, the reaction formula of metal silicon and chlorine is: Si+2Cl2=SiCl4. The main reaction formula for producing zirconium tetrachloride by chlorination of zircon sand is: ZrSiO4+4C+4Cl2=ZrCl4+SiCl4+4CO. The chlorinated products and by-products are discharged from the top of the fluidized chlorination furnace, and the slag is discharged from the lower part of the fluidized chlorination furnace. This process is a continuous operation process of continuous feeding and continuous discharging. Metal silicon can be mixed with Chlorine gas r...
specific Embodiment 3
[0034] Crush zircon sand to 325 mesh, crush petroleum coke powder to 200 mesh, crush metal silicon to 325 mesh, and crush silicon carbide to 325 mesh, first mix zircon sand, petroleum coke powder, metal silicon and silicon carbide powder evenly At the same time, it is added to the boiling chlorination furnace, and chlorine gas is introduced to carry out the chlorination reaction. The feeding ratio of zircon sand, petroleum coke powder, metal silicon and silicon carbide is: 1:0.22:0.2:0.2. Keep the fluidized furnace temperature at 1100°C, the reaction formula of silicon carbide and chlorine gas is: SiC+2Cl2=SiCl4+C, the reaction formula of metal silicon and chlorine gas is: Si+2Cl2=SiCl4. The main reaction formula for producing zirconium tetrachloride by chlorination of zircon sand is: ZrSiO4+4C+4Cl2=ZrCl4+SiCl4+4CO. The chlorinated products and by-products are discharged from the top of the fluidized chlorination furnace, and the slag is discharged from the lower part of the ...
PUM
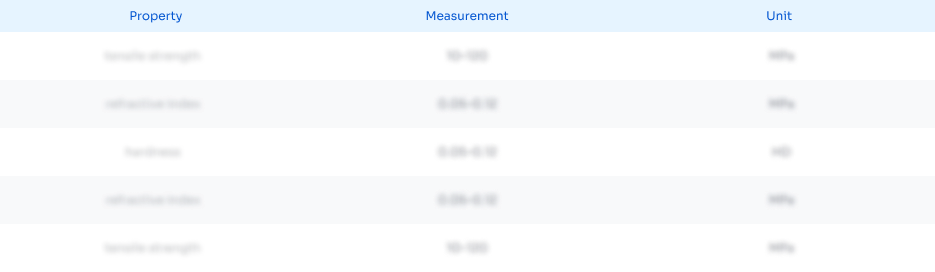
Abstract
Description
Claims
Application Information

- R&D
- Intellectual Property
- Life Sciences
- Materials
- Tech Scout
- Unparalleled Data Quality
- Higher Quality Content
- 60% Fewer Hallucinations
Browse by: Latest US Patents, China's latest patents, Technical Efficacy Thesaurus, Application Domain, Technology Topic, Popular Technical Reports.
© 2025 PatSnap. All rights reserved.Legal|Privacy policy|Modern Slavery Act Transparency Statement|Sitemap|About US| Contact US: help@patsnap.com