A method of preparing a homogeneous plain-color fabric based on color matching of primary color fibers
A technology of fibers and primary colors, applied in the field of preparing uniform plain fabrics, can solve problems such as inventory of unfavorable dye varieties, backlog of funds, etc., and achieve the effect of promoting promotion and application, easy management, and novel style
- Summary
- Abstract
- Description
- Claims
- Application Information
AI Technical Summary
Problems solved by technology
Method used
Image
Examples
Embodiment 1
[0047] Embodiment 1 (uniform plain woolen fabric)
[0048] 1) Select the primary color dyes: Lannasol-red 6G, Lannasol-yellow 4G, Lannasol-blue 2R, Lannasol-black CE four primary color dyes (purchased from Shanghai Huntsman Co., Ltd.), dyeing concentration Both are 3%, so as to obtain a color with higher saturation and a higher utilization rate of the dye.
[0049] 2) Preparation of primary color fiber: put the natural color wool top in the top dyeing machine, the bath ratio is 1:20, when the temperature of the dyeing bath is raised to 40°C, add 5% of the fiber quality of sodium sulfate, 1.5%-1.7% of the fiber quality Formic acid with a concentration of 85% and Abaiger relative to the dyeing bath capacity of 1g / L, after 5min, add the above-mentioned four primary color dyes and dye for 5min, heat to 98°C at a heating rate of 2°C / min, and fix the color 50min; when the temperature is lowered to 85°C, add soda ash and keep the temperature constant for 20min; after cooling down to...
Embodiment 2
[0054] Embodiment 2 (uniform plain cotton fabric)
[0055] 1) Select primary color dyes: preferably Norwich Red C-4B, Norwich Yellow C-5G, Norwich Turquoise Blue GN, Norwich Black B four primary color dyes (purchased from Shanghai Huntsman Co., Ltd.), dyeing The concentration is 3%, thus obtaining a color with higher saturation and a higher utilization rate of the dye.
[0056] 2) Preparation of primary color fibers: Dyeing in a bulk fiber dyeing machine with a bath ratio of 1:20. Use the constant temperature (60°C) dyeing method, add the above four dyes at 60°C, add 60g / l of salt after dyeing for 15min, add soda ash 18g / l after dyeing for 15min, fix the color for 30min, cool down after dyeing, take out Fiber, wash, tumble dry. Four-color primary color fibers are thus obtained. The colorimetric indexes of the obtained primary color fibers are listed in Table 2.
[0057] 3) Make uniform plain color fabrics: select magenta, yellow, blue, black and natural color five primary ...
Embodiment 3
[0061] Embodiment 3 (uniform plain colored polyester fabric)
[0062] 1) Choose magenta, yellow, cyan, black and natural polyester staple fibers (1.33dtex×38mm) provided by Jiangsu Xiake Environmental Color Spinning Co., Ltd., and their chromaticity indicators are listed in Table 3.
[0063] 2) Make uniform plain fabric: select five primary color fibers of magenta, yellow, cyan, black and natural color, and evenly mix them according to the mixing ratio of magenta:cyan=4:1. In the pre-spinning production, optimize the arrangement of fiber packs during fiber grabbing, increase the number of drawing frames to 3-5 times to achieve uniform mixing of multi-color fibers, and adopt conventional post-spinning and weaving processes to make rovings and take rings The spindle spinning machine spins 18.22tex × 2 polyester yarns, and the weaving dyeing and finishing process of Example 2 prepares uniform plain polyester fabric #5, such as Figure 5 As shown, its chromaticity value Lab is sh...
PUM
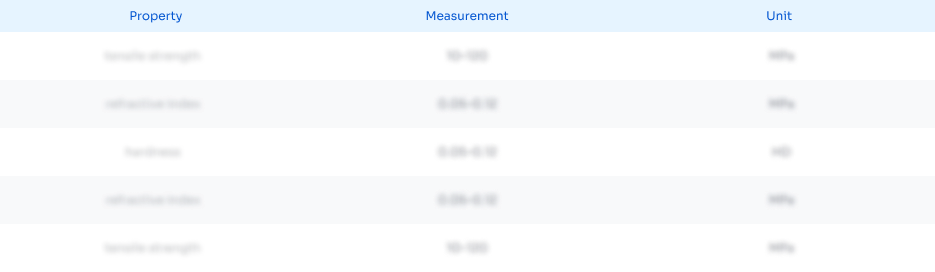
Abstract
Description
Claims
Application Information

- R&D Engineer
- R&D Manager
- IP Professional
- Industry Leading Data Capabilities
- Powerful AI technology
- Patent DNA Extraction
Browse by: Latest US Patents, China's latest patents, Technical Efficacy Thesaurus, Application Domain, Technology Topic, Popular Technical Reports.
© 2024 PatSnap. All rights reserved.Legal|Privacy policy|Modern Slavery Act Transparency Statement|Sitemap|About US| Contact US: help@patsnap.com