Production method of high-finish steel tube
A production method and high finish technology, applied in the field of steel pipe production, can solve the problems of steel pipe surface oxidation, high equipment cost, complex technology, etc., and achieve the effect of good surface quality, high equipment cost and high finish
- Summary
- Abstract
- Description
- Claims
- Application Information
AI Technical Summary
Problems solved by technology
Method used
Image
Examples
Embodiment Construction
[0017] A production method of a high-gloss steel pipe, which is made of No. 20 steel and a round pipe billet with a size of 38×3mm, includes the following steps:
[0018] 1. Tube billet heating: After passing the inspection, the φ50mm round tube billet is sent to the annular heating furnace for heating. The heating temperature is 1200°C±10°C, and the steel is tapped after holding for 50±5 minutes;
[0019] 2. Perforation: Select φ40mm plug, φ38mm ejector pin, adjust the distance between the rolls of the piercing machine to 40mm, the distance between the guide plates to 48mm, the extension of the plug to 31mm, and the reduction to 16% before perforating. The perforated capillary is φ52×4mm;
[0020] 3. Pickling, phosphating, and saponification: adjust the concentration of sulfuric acid in the pickling solution between 9% and 15%, and Fe 2+ ≤200g / L, keep the temperature of the pickling solution between 30°C and 65°C, pickle the φ52×4mm capillary with pickling, soak for 15 minute...
PUM
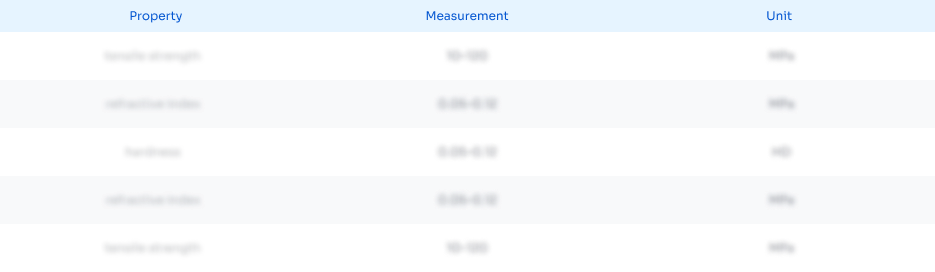
Abstract
Description
Claims
Application Information

- R&D
- Intellectual Property
- Life Sciences
- Materials
- Tech Scout
- Unparalleled Data Quality
- Higher Quality Content
- 60% Fewer Hallucinations
Browse by: Latest US Patents, China's latest patents, Technical Efficacy Thesaurus, Application Domain, Technology Topic, Popular Technical Reports.
© 2025 PatSnap. All rights reserved.Legal|Privacy policy|Modern Slavery Act Transparency Statement|Sitemap|About US| Contact US: help@patsnap.com