Preparation method of carbon fiber frictional particles
A technology of carbon fiber and chopped carbon fiber, which is applied in the field of preparation of carbon fiber friction particles, can solve problems such as difficulty in exerting excellent characteristics, achieve good infiltration, simple process, and reduce wear rate
- Summary
- Abstract
- Description
- Claims
- Application Information
AI Technical Summary
Problems solved by technology
Method used
Examples
Embodiment 1
[0029] In this embodiment, a method for preparing carbon fiber friction particles includes the following raw materials in parts by weight:
[0030] 90 parts of water, 0.3 part of methyl cellulose, 5 parts of carbon fiber treated with phenolic resin emulsion sizing, 5 parts of 100-mesh graphite powder, 5 parts of 100-mesh phenolic resin;
[0031] Concrete preparation method: comprise the following steps:
[0032] (1) Take 90 parts of water and 0.3 part of methylcellulose, put into a kneading pot with a discharge screw and fully dissolve to obtain a dissolving solution of methylcellulose;
[0033] (2) Then, 5 parts of carbon fiber, 5 parts of 100-mesh graphite powder, and 5 parts of 100-mesh phenolic resin treated with phenolic resin emulsion sizing are also poured into the kneading pot with a discharge screw in turn, stirred and dispersed uniform slurry formation;
[0034] (3) The slurry is extruded through the discharge screw of the kneading pot, dropped on the steel belt co...
Embodiment 2
[0040] In this embodiment, a method for preparing carbon fiber friction particles includes the following raw materials in parts by weight:
[0041] 100 parts of water, 2 parts of methyl cellulose, 10 parts of carbon fiber sizing treated with phenolic resin emulsion, 20 parts of 200-mesh graphite powder, 10 parts of 200-mesh phenolic resin;
[0042] Concrete preparation method: comprise the following steps:
[0043] (1) Take 100 parts of water and 2 parts of methylcellulose, put into a kneading pot with a discharge screw and fully dissolve to obtain a dissolving solution of methylcellulose;
[0044] (2) Then, 10 parts of carbon fiber, 20 parts of 200-mesh graphite powder, and 10 parts of 200-mesh phenolic resin that have been treated with phenolic resin emulsion sizing are also poured into the kneading pot with a discharge screw in turn, stirred and dispersed uniform slurry formation;
[0045] (3) Extrude the slurry through the discharge screw of the kneading pot, drop it on th...
Embodiment 3
[0051] In this embodiment, a method for preparing carbon fiber friction particles includes the following raw materials in parts by weight:
[0052] 95 parts of water, 1 part of methyl cellulose, 8 parts of carbon fiber sizing treated with phenolic resin emulsion, 15 parts of 150-mesh graphite powder, and 8 parts of 150-mesh phenolic resin.
[0053] Concrete preparation method: comprise the following steps:
[0054] (1) Take 95 parts of water and 1 part of methyl cellulose, put them into a kneading pot with a discharge screw and fully dissolve to obtain a dissolving solution of methyl cellulose;
[0055] (2) Then, 8 parts of carbon fiber, 15 parts of 150-mesh graphite powder, and 8 parts of 150-mesh phenolic resin that have been treated with phenolic resin emulsion sizing are also poured into the kneading pot with a discharge screw in turn, stirred and dispersed uniform slurry formation;
[0056] (3) Extrude the slurry through the discharge screw of the kneading pot, drop it ...
PUM
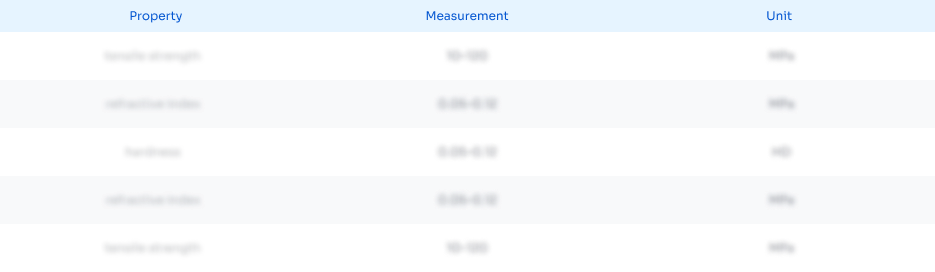
Abstract
Description
Claims
Application Information

- Generate Ideas
- Intellectual Property
- Life Sciences
- Materials
- Tech Scout
- Unparalleled Data Quality
- Higher Quality Content
- 60% Fewer Hallucinations
Browse by: Latest US Patents, China's latest patents, Technical Efficacy Thesaurus, Application Domain, Technology Topic, Popular Technical Reports.
© 2025 PatSnap. All rights reserved.Legal|Privacy policy|Modern Slavery Act Transparency Statement|Sitemap|About US| Contact US: help@patsnap.com