Modified phenolic resin, preparation process thereof and brake pad cementing agent prepared by using same
A technology of phenolic resin and preparation process, applied in the field of brake pads, can solve the problem of insignificant increase in thermal decomposition temperature of phenolic resin, and achieve the effects of small variation range of friction coefficient, small thermal recession, and excellent high temperature friction and wear performance.
- Summary
- Abstract
- Description
- Claims
- Application Information
AI Technical Summary
Problems solved by technology
Method used
Image
Examples
preparation example Construction
[0034] The preparation technology of modified phenolic resin provided by the invention comprises the following steps:
[0035] 1) Add phenol, formaldehyde aqueous solution, tung oil accounting for 10-15% by weight of phenol and dispersant accounting for 0.5-1.5% by weight of phenol into the reaction vessel, and then add 20-45% of the weight of phenol into the reaction vessel Nanoparticles in parts by weight to obtain the first mixed solution. Wherein, the reaction of phenol and formaldehyde aqueous solution obtains the phenolic resin, and the proportion relationship of its weight is the same as the existing one.
[0036] 2) heating the first mixed solution to obtain a second mixed solution.
[0037] 3) Add an alkali solution to the second mixed solution to adjust the pH to 8-9, and control the temperature at 80-105° C.; vacuum dehydration until the viscosity is 2.0-5.0 Pa. seconds, and then cool to form a solid resin to obtain the modified Phenolic Resin.
[0038] Wherein, ...
Embodiment 1
[0046] Get respectively 8 kilograms of brake pad adhesive (this brake pad adhesive is the brake pad adhesive obtained by the above-mentioned process, the following examples are referred to as brake pad adhesive), reinforcing material (the reinforcing material is copper wool, silicate Fiber or its combination, the following examples are referred to as reinforcing material) 18 kilograms, abrasive (abrasive is iron oxide, zircon stone or its combination, following example is referred to as abrasive) 13 kilograms, lubricant (lubricant is graphite, vulcanized Antimony or its combination, hereinafter referred to as lubricant) 15 kilograms, filler (filler is vermiculite, fluorite, barite or its combination, hereinafter referred to as filler) 25 kilograms. After the materials are uniformly mixed in the mixer, the brake pads are obtained by hot pressing forming technology. When the temperature is higher than 400°C, the phenomenon of thermal decay is not obvious, the braking performance...
Embodiment 2
[0048] Take 12 kg of brake pad adhesive, 30 kg of reinforcing material, 17 kg of abrasive, 25 kg of lubricant, and 50 kg of filler. After the materials are uniformly mixed in the mixer, the brake pads are obtained by hot pressing forming technology. When the temperature is higher than 400°C, the phenomenon of thermal decay is not obvious, the braking performance is stable, the range of friction coefficient is small, Δμ4 mg / Nm, the high temperature friction and wear performance of the brake pad is excellent.
PUM
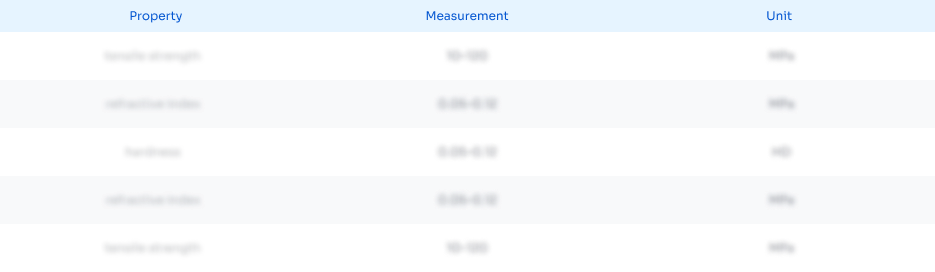
Abstract
Description
Claims
Application Information

- R&D Engineer
- R&D Manager
- IP Professional
- Industry Leading Data Capabilities
- Powerful AI technology
- Patent DNA Extraction
Browse by: Latest US Patents, China's latest patents, Technical Efficacy Thesaurus, Application Domain, Technology Topic, Popular Technical Reports.
© 2024 PatSnap. All rights reserved.Legal|Privacy policy|Modern Slavery Act Transparency Statement|Sitemap|About US| Contact US: help@patsnap.com