Preparation method for silane-modified moisture-curable polyurethane hot melt adhesive
A technology of polyurethane hot melt adhesive and silane modification, which is applied in the direction of polyurea/polyurethane adhesive, adhesive, adhesive type, etc. Fully respond to problems such as low wettability of waterproof fabrics, and achieve the effect of improving washing and peeling resistance, enhancing van der Waals force, and broadening application fields and development space.
- Summary
- Abstract
- Description
- Claims
- Application Information
AI Technical Summary
Problems solved by technology
Method used
Image
Examples
Embodiment 1
[0025] Install a thermometer, mechanical stirring, condenser and nitrogen inlet tube on a 1000mL four-necked flask, weigh 160g of polyoxypropylene diol (number average molecular weight 1000), polyethylene adipate diol (number average molecular weight 4000) ) 45.25g, acrylic resin 60g, antioxidant 1010 0.64g, sodium distyryl biphenyl disulfonate 0.8g, then heated to 120-140°C, stirred and mixed, while degassing under reduced pressure for 2h (absolute pressure 100Pa), cooling down To 90°C; under nitrogen protection, add 62.5 g of 4,4′-diphenylmethane diisocyanate, 0.1 g of the compound of stannous octoate and bismorpholine diethyl ether in a mass ratio of 1:1, 85~95°C Under the conditions, the reaction time was 45 min. Under the protection of nitrogen, 2.4 g of 1,4-butanediol was added, and the mixture was stirred at 85-95°C for 1 h. The above prepolymer was discharged under the protection of nitrogen, sealed and packaged, and aged at 85°C for 6 hours to obtain the product, num...
Embodiment 2
[0027] Install a thermometer, mechanical stirring, condenser and nitrogen gas inlet tube on a 1000mL four-neck flask, weigh 160g of polyethylene glycol (number average molecular weight 1250), polybutylene adipate diol (number average molecular weight 1000) 45.25g, phenolic resin 60g, antioxidant 1010 0.64g, triazineaminostilbene 0.8g, then heated to 120-140°C, stirred and mixed, and degassed under reduced pressure for 2 hours (absolute pressure 100Pa), cooled to 90°C ; Add 62.5 g of 2,4′-diphenylmethane diisocyanate under nitrogen protection, 0.1 g of the compound of stannous octoate and bismorpholine diethyl ether in a mass ratio of 1:1, and under the condition of 85~95°C, React for 45 min. Under the protection of nitrogen, add 2.4g of 1.6-hexanediol and 2g of 3-trimethoxysilylpropyl isocyanurate, stir at 85~95°C for 1 hour and discharge the material, and put the above prepolymer under nitrogen Discharge under protection and seal the package, and ripen at 85°C for 6 hours to...
Embodiment 3
[0029] Install a thermometer, mechanical stirring, condenser and nitrogen inlet tube on a 1000mL four-necked flask, weigh polytetrahydrofuran ether glycol (number average molecular weight 2000) 160g, poly(ethylene terephthalate) glycol (number average molecular weight 4000) 16g, C 5 -C 9 Petroleum resin 32g, antioxidant 1010 0.32g, phthalimide 0.08g, then heated to 120-140°C, stirred and mixed, and degassed under reduced pressure for 2 hours (absolute pressure 300Pa), cooled to 90°C; nitrogen protection Add 16 g of 2,2′-diphenylmethane diisocyanate, 0.08 g of the mixture of stannous octoate and bismorpholine diethyl ether at a mass ratio of 1:1, and react for 45 minutes at 85~95°C . Under the protection of nitrogen, add 1.6g of glycerin and 4g of 3-ureapropyltriethoxysilane, stir and react at a high speed at 85~95°C for 1 h to discharge, and discharge the above prepolymer under the protection of nitrogen and seal the package. Aged at 85°C for 6 hours to obtain the product, ...
PUM
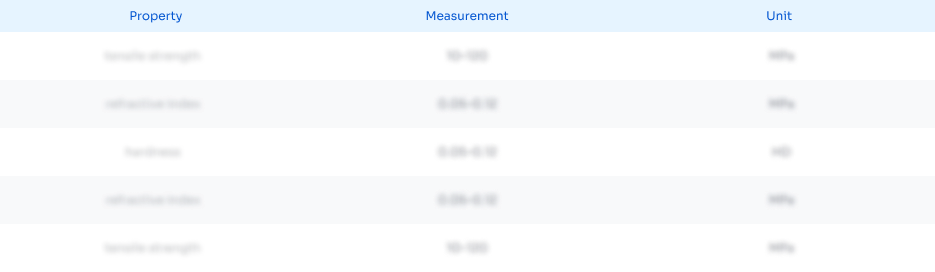
Abstract
Description
Claims
Application Information

- Generate Ideas
- Intellectual Property
- Life Sciences
- Materials
- Tech Scout
- Unparalleled Data Quality
- Higher Quality Content
- 60% Fewer Hallucinations
Browse by: Latest US Patents, China's latest patents, Technical Efficacy Thesaurus, Application Domain, Technology Topic, Popular Technical Reports.
© 2025 PatSnap. All rights reserved.Legal|Privacy policy|Modern Slavery Act Transparency Statement|Sitemap|About US| Contact US: help@patsnap.com