A steel bar for high-strength prestressed concrete and its production process
A production process and prestressing technology, which is applied in the field of smelting, can solve problems such as hidden dangers in quality, economic loss, and poor performance of steel bars, and achieve the effects of strong resistance to hysteresis fracture, ensuring product qualification rate, and good upsetting performance
- Summary
- Abstract
- Description
- Claims
- Application Information
AI Technical Summary
Problems solved by technology
Method used
Examples
Embodiment 1
[0040] This embodiment provides a steel bar for high-strength prestressed concrete, the chemical composition of which is: C: 0.25%, Si: 1.65%, Mn: 0.20%, Cr: 0.08%, Mo: 0.35%, V: 0.25 %, Nb: 0.08%, Ti: 0.50%, Ni: 0.25%, Ca: 0.30%, S: 0.025%, P: 0.010%, Cu: 0.15%, composite rare earth: 0.20%, and the balance is Fe;
[0041] The composition of compound rare earth is calculated by mass percentage: holmium: 5%, gadolinium: 8%, yttrium: 9%, cerium: 20%, praseodymium: 23%, neodymium: 12%, dysprosium: 14%, and the rest is lanthanum, The sum of the above components is 100%.
[0042] The production process of the above-mentioned high-strength prestressed concrete steel rod, the specific production process is as follows:
[0043] (1) The above components are used as raw materials through converter smelting, refining treatment, and continuous casting to obtain billets, and then the billets are heated to 1000°C through a walking heating furnace, and the heated billets are taken out of th...
Embodiment 2
[0057] This embodiment provides a steel bar for high-strength prestressed concrete, and its weight percentage chemical composition is: C: 0.20%, Si: 1.50%, Mn: 0.50%, Cr: 0.07%, Mo: 0.30%, V: 0.35 %, Nb: 0.05%, Ti: 0.42%, Ni: 0.15%, Ca: 0.25%, S: 0.015%, P: 0.015%, Cu: 0.20%, composite rare earth: 0.15%, and the balance is Fe;
[0058] The composition of compound rare earth is calculated by mass percentage: holmium: 8%, gadolinium: 9%, yttrium: 8%, cerium: 18%, praseodymium: 25%, neodymium: 15%, dysprosium: 11%, and the rest is lanthanum, The sum of the above components is 100%.
[0059] The production process of the above-mentioned high-strength prestressed concrete steel rod, the specific production process is as follows:
[0060] (1) The above components are used as raw materials through converter smelting, refining treatment, and continuous casting to obtain billets, and then the billets are heated to 1250°C through a walking heating furnace, and the heated billets are ta...
Embodiment 3
[0074] This embodiment provides a steel rod for high-strength prestressed concrete, the chemical composition of which is: C: 0.22%, Si: 1.85%, Mn: 0.35%, Cr: 0.09%, Mo: 0.33%, V: 0.30 %, Nb: 0.07%, Ti: 0.61%, Ni: 0.18%, Ca: 0.40%, S: 0.020%, P: 0.025%, Cu: 0.15%, composite rare earth: 0.30%, and the balance is Fe;
[0075] The composition of compound rare earth is calculated by mass percentage: holmium: 7%, gadolinium: 10%, yttrium: 10%, cerium: 15%, praseodymium: 24%, neodymium: 13%, dysprosium: 13%, and the rest is lanthanum, The sum of the above components is 100%.
[0076] The production process of the above-mentioned high-strength prestressed concrete steel rod, the specific production process is as follows:
[0077](1) The above-mentioned components are used as raw materials through converter smelting, refining treatment, and continuous casting to obtain billets, and then the billets are heated to 1500°C through a walking heating furnace, and the heated billets are take...
PUM
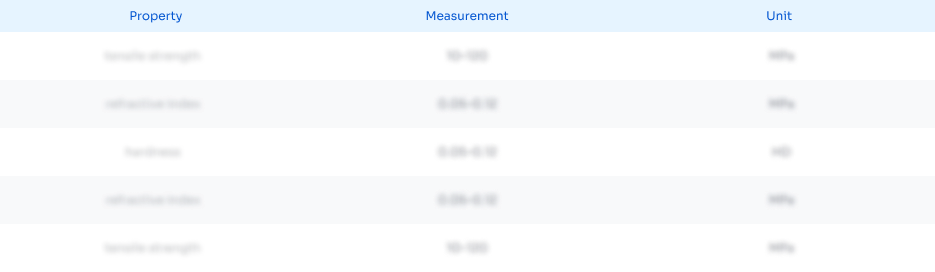
Abstract
Description
Claims
Application Information

- R&D
- Intellectual Property
- Life Sciences
- Materials
- Tech Scout
- Unparalleled Data Quality
- Higher Quality Content
- 60% Fewer Hallucinations
Browse by: Latest US Patents, China's latest patents, Technical Efficacy Thesaurus, Application Domain, Technology Topic, Popular Technical Reports.
© 2025 PatSnap. All rights reserved.Legal|Privacy policy|Modern Slavery Act Transparency Statement|Sitemap|About US| Contact US: help@patsnap.com