Method for Improving Resistance to Hydrogen-Induced Delayed Fracture of Fe-mn-al-c Lightweight Steel
A fe-mn-al-c, delayed fracture technology, applied in the field of light steel, can solve the problems of delayed fracture of high-strength light steel, car factory economy, reputation loss, serious hydrogen embrittlement sensitivity, etc., to achieve low price, Small investment, the effect of improving the resistance to hydrogen-induced delayed fracture
- Summary
- Abstract
- Description
- Claims
- Application Information
AI Technical Summary
Problems solved by technology
Method used
Examples
Embodiment 1
[0037] C: 0.9%, Al: 9.0%, Mn: 26.0%, Cu: 1.0%, and the rest are Fe and inevitable impurities (wherein, Si: ≤ 0.1%, P ≤ 0.03%, S: ≤ 0.005%).
[0038] The raw materials are weighed according to the preset ratio, and then placed in a vacuum intermediate frequency induction furnace to be smelted, cast into ingots, and cooled to room temperature; forging treatment: heating to 1050 ° C before forging, holding for 1.5 h, forging temperature 950 ° C, forging After air cooling to room temperature; hot rolling treatment: heating to 1050 ℃ before hot rolling, holding for 1 hour, starting rolling temperature 1000 ℃, final rolling temperature 850 ℃, reduction rate of 20% each time, rolling 9 passes; cold rolling treatment : Heating to 950℃ before cold rolling, holding for 1h, the reduction rate of each time is 5%, rolling 13 times; the aging treatment temperature is 450℃, the aging time is 3h, and the water is cooled to room temperature.
Embodiment 2
[0040] C: 1.0%, Al: 10.0%, Mn: 28.0%, Cu: 3.0%, and the rest are Fe and inevitable impurities (wherein, Si: ≤ 0.1%, P ≤ 0.03%, S: ≤ 0.005%). The raw materials are weighed according to the preset ratio, and then placed in a vacuum intermediate frequency induction furnace to be smelted, cast into ingots, and cooled to room temperature; forging treatment: heating to 1050 ° C before forging, holding for 1.5 h, forging temperature 950 ° C, forging After air cooling to room temperature; hot rolling treatment: heating to 1050 ℃ before hot rolling, holding for 1 hour, starting rolling temperature 1000 ℃, final rolling temperature 850 ℃, reduction rate of 20% each time, rolling 9 passes; cold rolling treatment : Heating to 950℃ before cold rolling, holding for 1h, the reduction rate of each time is 5%, rolling 13 times; aging treatment temperature is 550℃, aging time is 3h, and air-cooled to room temperature.
Embodiment 3
[0042] C: 1.2%, Al: 11.0%, Mn: 31.0%, Cu: 5.0%, and the rest are Fe and inevitable impurities (wherein, Si: ≤ 0.1%, P ≤ 0.03%, S: ≤ 0.005%). The raw materials are weighed according to the preset ratio, and then placed in a vacuum intermediate frequency induction furnace to be smelted, cast into ingots, and cooled to room temperature; forging treatment: heating to 1050 ° C before forging, holding for 1.5 h, forging temperature 950 ° C, forging After air cooling to room temperature; hot rolling treatment: heating to 1050 ℃ before hot rolling, holding for 1 hour, starting rolling temperature 1000 ℃, final rolling temperature 850 ℃, reduction rate of 20% each time, rolling 9 passes; cold rolling treatment : Heating to 950℃ before cold rolling, holding for 1h, the reduction rate of each time is 5%, rolling 13 passes; the aging treatment temperature is 620℃, the aging time is 10h, and the furnace is cooled to room temperature.
PUM
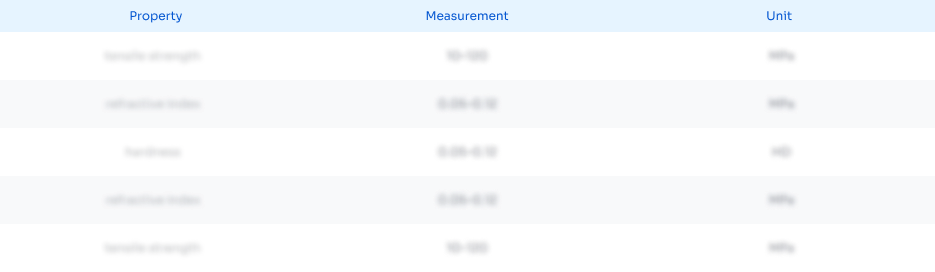
Abstract
Description
Claims
Application Information

- R&D
- Intellectual Property
- Life Sciences
- Materials
- Tech Scout
- Unparalleled Data Quality
- Higher Quality Content
- 60% Fewer Hallucinations
Browse by: Latest US Patents, China's latest patents, Technical Efficacy Thesaurus, Application Domain, Technology Topic, Popular Technical Reports.
© 2025 PatSnap. All rights reserved.Legal|Privacy policy|Modern Slavery Act Transparency Statement|Sitemap|About US| Contact US: help@patsnap.com