Preparation method for poly(p-phenylene terephthamide) membrane
The technology of poly-p-phenylene terephthalamide and terephthaloyl chloride is applied in the field of preparation of poly-p-phenylene terephthalamide film, which can solve the problems of difficult process control and high production cost, and achieves the Improve film-forming performance and pore-forming performance, process safety, and optimize the effect of production processes
- Summary
- Abstract
- Description
- Claims
- Application Information
AI Technical Summary
Problems solved by technology
Method used
Examples
preparation example Construction
[0011] The preparation method of the poly-p-phenylene terephthalamide film that the present invention proposes comprises the following steps:
[0012] (1) Polymerization: Add solvent N to methylpyrrolidone (hereinafter referred to as NMP) into the reactor, add polymerization aids and surfactants while stirring under nitrogen protection and a rotating speed of 50 to 300 rpm, and heat the reactor to 70 ~100°C and constant temperature until the auxiliary agent and surfactant are dissolved, then the reactor is cooled to 0-30°C, and the first polymerized monomer p-phenylenediamine (hereinafter referred to as PPD) is added to make the molar concentration of p-phenylenediamine After the p-phenylenediamine is completely dissolved, the temperature of the reactor is lowered to -15-10°C, and then the second polymerization monomer terephthaloyl chloride (hereinafter referred to as TPC) is added for polymerization, so that the p-phenylenediamine The molar concentration of phthaloyl chlorid...
Embodiment 1
[0020] 1) Add 100mL NMP to a 300ml reactor, add 10g of polymerization aid CaCl under nitrogen protection and stirring 2 and 5g of polyethylene glycol (PEG) with a molecular weight of 2100, heated to 100°C to dissolve the auxiliary agent and surfactant. To be CaCl 2 After the PEG and PEG are completely dissolved, the system is lowered to 15°C with an ice-water bath, and then 4.326g of p-phenylenediamine (PPD) is added to dissolve. After the PPD is completely dissolved, 8.178g of terephthaloyl chloride (TPC) is added and stirred at a high speed (2000r / min ) for polymerization, keep an ice-water bath during the polymerization process, and keep the system temperature not exceeding 70°C;
[0021] 2) The above polycondensation reaction proceeds until the system forms a jelly body and the Weissenberg effect occurs, stop stirring, remove the ice-water bath, take out 5 g of the jelly body and add 200 ml of NMP, stir the swollen jelly body for 5 minutes quickly with a tissue grinder, a...
Embodiment 2
[0024] 1) Add 100mL NMP to a 300ml reactor, add 8g of polymerization aid LiCl and 5g of polyethylene glycol (PEG) with a molecular weight of 2100 and an ethyl end group under nitrogen protection and stirring, and heat to 100°C to make the aid and The surfactant dissolves. After LiCl and PEG are completely dissolved, use an ice-water bath to lower the system to 10°C, then add 4.326g of p-phenylenediamine (PPD) to dissolve, and then add 8.160g of terephthaloyl chloride (TPC) after PPD is completely dissolved and stir at a high speed (2000r / min) to carry out polymerization, keep an ice-water bath during the polymerization process, and keep the system temperature not exceeding 60°C;
[0025]2) The above polycondensation reaction is carried out until the system forms a jelly body and the Weissenberg effect occurs, stop stirring, remove the ice-water bath, take out 5g of the jelly body and add 300ml of NMP, stir the swollen jelly body for 5 minutes with a tissue pulverizer, break u...
PUM
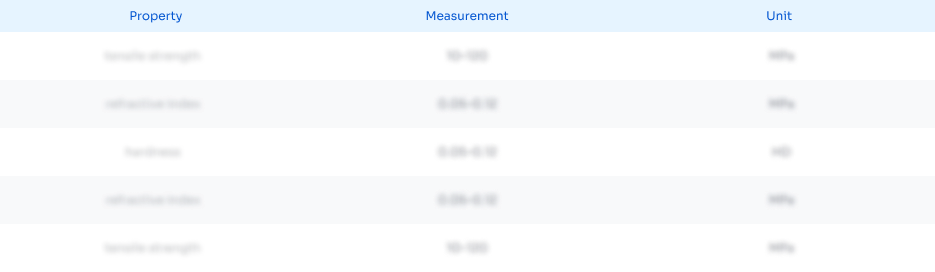
Abstract
Description
Claims
Application Information

- R&D Engineer
- R&D Manager
- IP Professional
- Industry Leading Data Capabilities
- Powerful AI technology
- Patent DNA Extraction
Browse by: Latest US Patents, China's latest patents, Technical Efficacy Thesaurus, Application Domain, Technology Topic, Popular Technical Reports.
© 2024 PatSnap. All rights reserved.Legal|Privacy policy|Modern Slavery Act Transparency Statement|Sitemap|About US| Contact US: help@patsnap.com