Method for separating and recycling vanadium and chromium from vanadium and chromium-containing material
A technology for separation and recovery of materials, applied in the field of metallurgy, can solve the problems of high cost, complex process, complicated operation, etc., and achieve the effects of low production cost, good separation effect and short process flow
- Summary
- Abstract
- Description
- Claims
- Application Information
AI Technical Summary
Problems solved by technology
Method used
Examples
Embodiment 1
[0034]Get 200g of green mud formed in the purification process of vanadium slag extracting vanadium wastewater, add sulfuric acid according to 1.5 times of the stoichiometric amount of chromium sulfate and vanadyl sulfate formed by vanadium and chromium respectively, and oxidize tetravalent vanadium into pentavalent vanadium according to the chemical reaction Add potassium dichromate as an oxidizing agent to 1.5 times the measured quantity, mix well, and mature at 120°C for 2.5h. Add water to the matured material at a solid-to-liquid ratio of 1:1.5g / mL, soak at room temperature for 4 hours, stir and add ammonia water to adjust the pH to 2.5, react at 90°C for 1.5 hours, and filter to obtain filtrate and filter residue. The resulting filtrate was neutralized with sodium hydroxide to a pH of 6.2, and the supernatant and bottom sludge were obtained by standing still. The pH of the bottom sludge was adjusted to 13.2 by adding NaOH, stirred at 65°C for 1 hour, filtered to obtain hyd...
Embodiment 2
[0036] Get 100g of the vanadium-chromium concentrate obtained after reducing and removing iron from the high-chromium vanadium slag, add sulfuric acid by 1 times of the stoichiometric number of chromium sulfate and vanadyl sulfate formed by vanadium and chromium respectively, and add the Cr-containing compound obtained in Example 1. The washing solution of (VI) is used as an oxidizing agent, and simultaneously forms (NH 4 ) 2 V 6 o 12 Add ammonium sulfate twice the stoichiometric number, add water, mix well, and roast at low temperature at 210°C for 2h. The obtained calcined sand was stirred with water at a solid-to-liquid ratio of 1:2 g / mL, and NaOH was added to adjust the pH to 3.2, reacted at 80°C for 2.5 hours, and filtered to obtain filtrate and filter residue. The resulting filtrate was neutralized with ammonia water until the pH was 7.8, filtered to obtain hydrated chromium oxide, dried at 110°C, crushed and ground to obtain chromium oxide containing Cr 2 o 3 A 37....
Embodiment 3
[0038] Get the vanadium-chromium-titanium slag 5000g that high-chromium type vanadium-titanium magnetite concentrate reduces and removes iron and obtains, according to wherein vanadium and chromium respectively form 2 times of the stoichiometric number of chromium sulfate and vanadyl sulfate, add the sulfuric acid of 1:1, and press wherein Low-valent vanadium is oxidized to 5 times the stoichiometric number of pentavalent vanadium. Add sodium dichromate as an oxidant, and at the same time form pentavalent vanadium (NH 4 ) 2 V 6 o 12 Add ammonium sulfate to 6 times the stoichiometric number, mix well, and roast at a low temperature of 240°C for 1.5h. The obtained calcined sand is stirred with water according to the solid-to-liquid ratio of 1:2.5g / mL, and NaHCO is added 3 Adjust the pH to 2.5, react at 100°C for 1 hour, and filter to obtain the filtrate and filter residue. Add sodium carbonate to the resulting filtrate to neutralize to pH 6.9, filter to obtain hydrated chrom...
PUM
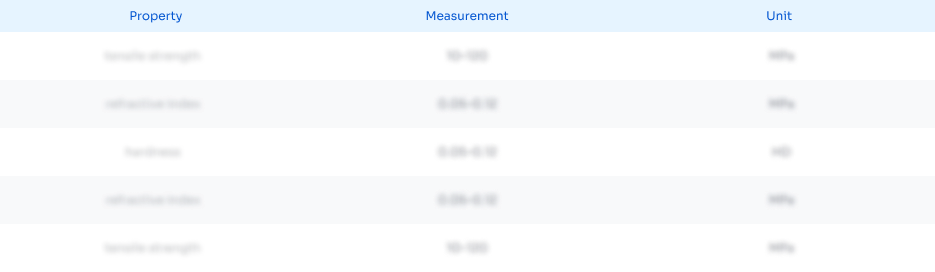
Abstract
Description
Claims
Application Information

- R&D
- Intellectual Property
- Life Sciences
- Materials
- Tech Scout
- Unparalleled Data Quality
- Higher Quality Content
- 60% Fewer Hallucinations
Browse by: Latest US Patents, China's latest patents, Technical Efficacy Thesaurus, Application Domain, Technology Topic, Popular Technical Reports.
© 2025 PatSnap. All rights reserved.Legal|Privacy policy|Modern Slavery Act Transparency Statement|Sitemap|About US| Contact US: help@patsnap.com