Unwinding and stacking method and equipment for brittle, weak and strong fibers
A brittle and fiber technology, applied in the field of fiber structure manufacturing technology and equipment, can solve the problems such as heating of fiber materials that are disordered and irregular, low fiber structure regularity, excessive molecular chain breakage, etc., and achieves beautiful and concise appearance and exquisite structure design. , the effect of tempo synchronization
- Summary
- Abstract
- Description
- Claims
- Application Information
AI Technical Summary
Problems solved by technology
Method used
Image
Examples
Embodiment 1
[0040] A method for unwinding and stacking brittle, weak, and strong fibers using the equipment described in the present invention, comprising the following steps: obtaining the speed of the godet roller, deviation correction, Speed and dynamic correction parameters; X-axis direction and Y-axis direction interpolation speed parameters match the unwinding fiber filament speed parameters, and the X-axis direction and Y-axis direction interpolation speed parameters are determined by the controller 4 according to The unwinding speed of the fiber, the diameter of the winding of the fiber, and the superposition spacing in the X-axis direction and the Y-axis direction are calculated;
[0041] Calculate the unwinding line speed to generate the tray speed parameter; the controller 4 reads the tray speed parameter for control and calculation, and obtains the unwinding speed, reciprocating speed and reciprocating stroke; wherein the controller 4 passes the The signal of the deflection ...
Embodiment 2
[0043] The fiber filament is 2 kilometers long, and the winding head is made of plastic material. The above-mentioned airflow concentrator exerts a pressure of 0.5 MPa on a single fiber and draws it. The fiber is a carbon fiber polycarbosilane series fiber, and the tray is a ceramic tray. Others are with embodiment 1.
Embodiment 3
[0045] The fiber filament is 3 kilometers long, and the winding head is made of plastic material. The above-mentioned airflow concentrator exerts a pressure of 0.8 MPa on a single fiber filament for traction, the fiber filament is pitch fiber, and the tray is a carbon tray. Others are with embodiment 1.
PUM
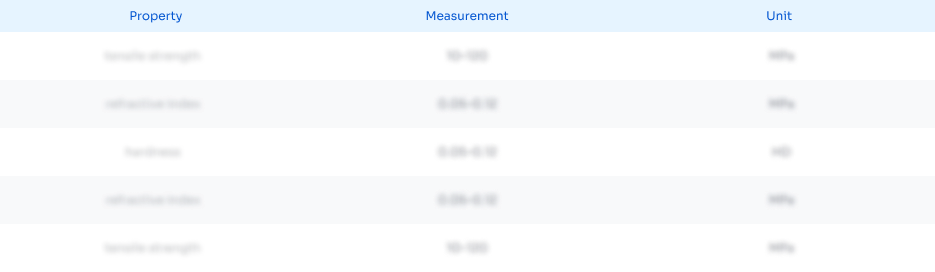
Abstract
Description
Claims
Application Information

- R&D Engineer
- R&D Manager
- IP Professional
- Industry Leading Data Capabilities
- Powerful AI technology
- Patent DNA Extraction
Browse by: Latest US Patents, China's latest patents, Technical Efficacy Thesaurus, Application Domain, Technology Topic, Popular Technical Reports.
© 2024 PatSnap. All rights reserved.Legal|Privacy policy|Modern Slavery Act Transparency Statement|Sitemap|About US| Contact US: help@patsnap.com