Method for recycling lithium iron phosphate wastes in manufacturing link of lithium iron phosphate batteries
A lithium iron phosphate battery, lithium iron phosphate technology, applied in battery recycling, recycling technology, waste collector recycling and other directions, can solve the problems of low recycling rate, production loss, increase production cost, etc., to achieve recycling rate High, low cost, good electrochemical performance
- Summary
- Abstract
- Description
- Claims
- Application Information
AI Technical Summary
Problems solved by technology
Method used
Image
Examples
Embodiment 1
[0030] Neatly stack 20Kg of lithium iron phosphate cathode sheets to be recovered in a stainless steel tray, put them into a muffle furnace, heat up to 500°C, and bake for 2 hours. The binder PVDF will decompose and fail, and the active material lithium iron phosphate and conductive The conductive agent powder completely falls off from the aluminum foil of the current collector; then, put the obtained powder into a muffle furnace, bake at 700°C for 5 hours to remove the conductive agent, and pass through a 250-mesh sieve to obtain lithium iron phosphate powder. Lithium iron phosphate material contains other impurities, poor electrochemical performance, poor availability, and needs to be purified. Take 7Kg from the above-mentioned lithium iron phosphate powder, wash 3 times with 70 Kg of deionized water, add 40 Kg of 1% ethanol solution, stir into a uniform suspension, then add 9.8 Kg of iron nitrate, 4.567 Kg Ammonium dihydrogen phosphate, 1.703 Kg lithium hydroxide monohydrat...
Embodiment 2
[0032] Neatly stack 10Kg of lithium iron phosphate cathode sheets to be recovered in a stainless steel tray, put them into a muffle furnace, heat up to 600°C, and bake for 3 hours. The binder LA133 will decompose and fail, and the active material lithium iron phosphate and conductive The conductive agent powder is completely detached from the current collector aluminum foil; then, the obtained powder is put into a muffle furnace, baked at 800°C for 4 hours to remove the conductive agent, and passed through a 325-mesh screen to obtain lithium iron phosphate powder. Take 2Kg of lithium powder, wash 3 times with 24Kg of deionized water, add 16Kg of 1% ethanol solution, stir into a uniform suspension, then add 4.895Kg of iron sulfate, 2.818 Kg of diammonium hydrogen phosphate, 0.923 Kg of lithium carbonate, mixed with zirconia balls, ball milled for 6 hours, and vacuum-dried at 100°C. Finally, put it in a nitrogen-protected tube furnace and bake it at 650°C for 6 hours, and then c...
PUM
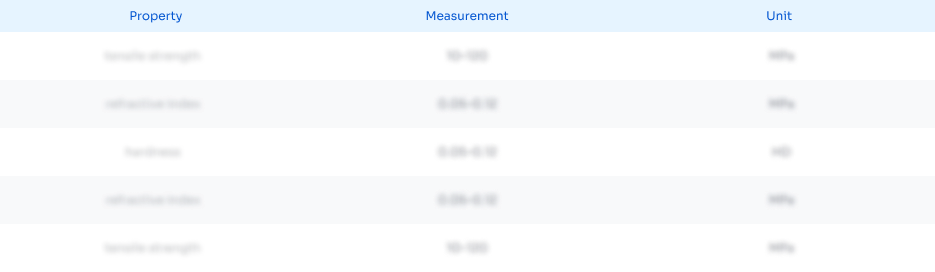
Abstract
Description
Claims
Application Information

- Generate Ideas
- Intellectual Property
- Life Sciences
- Materials
- Tech Scout
- Unparalleled Data Quality
- Higher Quality Content
- 60% Fewer Hallucinations
Browse by: Latest US Patents, China's latest patents, Technical Efficacy Thesaurus, Application Domain, Technology Topic, Popular Technical Reports.
© 2025 PatSnap. All rights reserved.Legal|Privacy policy|Modern Slavery Act Transparency Statement|Sitemap|About US| Contact US: help@patsnap.com