Grinder gear lubricating grease and preparation method thereof
A gear grease and grinding machine technology, applied in the field of grease, can solve the problems of not being able to maintain lubrication for a long time, waste of manpower, equipment downtime, etc. effect of life
- Summary
- Abstract
- Description
- Claims
- Application Information
AI Technical Summary
Problems solved by technology
Method used
Examples
Embodiment 1
[0024] (1) Weigh 18kg of polypropylene wax, 12kg of ammonium sulfate, 3kg of epoxypropyltriethylammonium chloride, 2kg of triethanolammonium salt, 0.25kg of vinyltriethoxysilane, and iso-triisostearyl titanate 0.25kg of propyl ester and 1kg of 2,6-di-tert-butyl-p-cresol, heated to 150°C, stirred for 1.5 hours, and cooled;
[0025] (2) Add 70 kg of paraffin base oil to the product of step 1, stir for 0.5 hour at a mechanical stirring rate of 1200 rpm, and grind repeatedly for 4 hours to obtain the grinder gear grease.
[0026] The performance test results of the prepared grinder gear grease are shown in Table 1.
Embodiment 2
[0028] (1) Weigh 10kg of polypropylene wax, 10kg of ammonium sulfate, 5kg of epoxypropyltriethylammonium chloride, 1kg of triethanolammonium salt, 1kg of vinyltriethoxysilane, and isopropyl triisostearyl titanate 1 kg of ester and 0.8 kg of 2,6-di-tert-butyl-p-cresol, heated to 180°C, stirred for 2 hours, and cooled;
[0029] (2) Add 85 kg of paraffin base oil to the product of step 1, stir for 1 hour at a mechanical stirring rate of 1400 rpm, and grind repeatedly for 4 hours to obtain the grinder gear grease.
[0030] The performance test results of the prepared grinder gear grease are shown in Table 1.
Embodiment 3
[0032] (1) Weigh 14kg of polypropylene wax, 15kg of ammonium sulfate, 4kg of epoxypropyltriethylammonium chloride, 2kg of triethanolammonium salt, 1kg of vinyltriethoxysilane, and isopropyl triisostearyl titanate 1kg of ester and 1kg of 2,6-di-tert-butyl-p-cresol, heated to 200°C, stirred for 1 hour, and cooled;
[0033] (2) Add 75 kg of trimethylolpropane ester to the product in step 1, stir for 0.5 hour at a mechanical stirring rate of 1500 rpm, and grind repeatedly for 2 hours to obtain the grinder gear grease.
[0034] The performance test results of the prepared grinder gear grease are shown in Table 1.
PUM
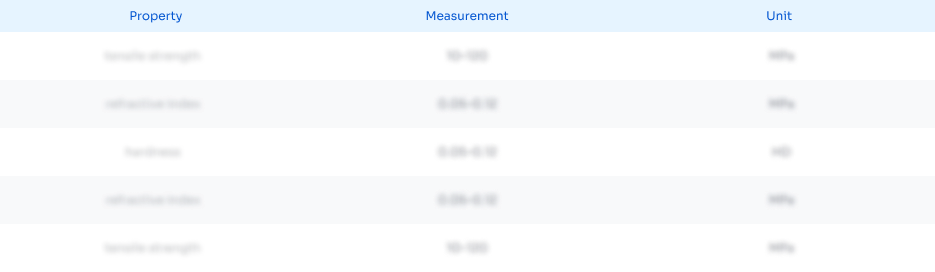
Abstract
Description
Claims
Application Information

- Generate Ideas
- Intellectual Property
- Life Sciences
- Materials
- Tech Scout
- Unparalleled Data Quality
- Higher Quality Content
- 60% Fewer Hallucinations
Browse by: Latest US Patents, China's latest patents, Technical Efficacy Thesaurus, Application Domain, Technology Topic, Popular Technical Reports.
© 2025 PatSnap. All rights reserved.Legal|Privacy policy|Modern Slavery Act Transparency Statement|Sitemap|About US| Contact US: help@patsnap.com