High polymer waterproofing agent and synthesis method and application thereof
A technology of polymer waterproofing and synthesis method, which is applied in the field of polymer waterproofing agent and its synthesis, can solve the problems of cracking, accelerated cement curing, and high cost of use, and achieves the effects of simple process route, improved compressive strength, and increased waterproof performance.
- Summary
- Abstract
- Description
- Claims
- Application Information
AI Technical Summary
Problems solved by technology
Method used
Image
Examples
Embodiment 1
[0024] (1) Preparation of intermediates: 100.0 grams of polyethylene glycol (molecular weight 600), 51.7 grams of oleic acid, and 1.2 grams of p-toluenesulfonic acid were put into the reactor, heated to 110°C, and kept for 4 hours to obtain oleic acid polymer. Glycol esters.
[0025] (2) Preparation of polymer waterproofing agent: 100 grams of step (1) gained oleic acid polyethylene glycol ester, 10.8 grams of acrylic acid are dissolved in 105 grams of water, evenly drip 25 grams of ammonium persulfate aqueous solution ( Concentration 5.5%), dropwise adding time 100 minutes, keep warm at 65°C for 3 hours after dropwise addition, then cool down to 45°C, add NaOH to neutralize, adjust system pH to 7-8, and obtain polymer waterproofing agent.
Embodiment 2
[0027] (1) Preparation of intermediates: 100.0 grams of polyethylene glycol (molecular weight 2400), 12.5 grams of oleic acid, and 1.2 grams of p-toluenesulfonic acid were put into the reactor, heated to 100°C, and kept for 4 hours to obtain oleic acid polymer Glycol esters.
[0028] (2) Preparation of polymer waterproofing agent: 100 grams of step (1) gained oleic acid polyethylene glycol ester, 3.0 grams of acrylic acid are dissolved in 110 grams of water, evenly drip 25 grams of ammonium persulfate aqueous solution ( Concentration 5.5%), dropwise adding time 100 minutes, keep warm at 65°C for 4 hours after dropwise addition, then cool down to 45°C, add NaOH to neutralize, adjust system pH to 7-8, and obtain polymer waterproofing agent.
[0029] Gel permeation chromatography test results (see figure 2 ) found that the molecular weight distribution of the sample was relatively uniform, with an average molecular weight of about 180,000.
Embodiment 3
[0031] (1) Preparation of intermediates: 100.0 grams of polyethylene glycol (molecular weight 10,000), 3.1 grams of oleic acid, and 1.7 grams of p-toluenesulfonic acid were put into the reactor, heated to 105°C, and kept for 5 hours to obtain oleic acid polymer. Glycol esters.
[0032] (2) Preparation of polymer waterproofing agent: 100 grams of step (1) gained oleic acid polyethylene glycol ester, 1.05 grams of acrylic acid are dissolved in 105 grams of water, evenly drip 23 grams of ammonium persulfate aqueous solution ( Concentration 6.0%), dropwise adding time 120 minutes, keep warm at 60°C for 2 hours after dropwise addition, then cool down to 45°C, add NaOH to neutralize, adjust system pH to 7-8, and obtain polymer waterproofing agent.
PUM
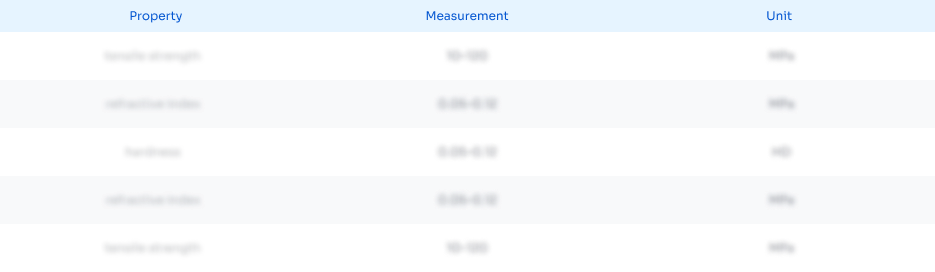
Abstract
Description
Claims
Application Information

- R&D
- Intellectual Property
- Life Sciences
- Materials
- Tech Scout
- Unparalleled Data Quality
- Higher Quality Content
- 60% Fewer Hallucinations
Browse by: Latest US Patents, China's latest patents, Technical Efficacy Thesaurus, Application Domain, Technology Topic, Popular Technical Reports.
© 2025 PatSnap. All rights reserved.Legal|Privacy policy|Modern Slavery Act Transparency Statement|Sitemap|About US| Contact US: help@patsnap.com