A kind of manufacturing method of baking varnish aluminum alloy plate
An aluminum alloy plate and a manufacturing method technology, applied in the field of aluminum alloy manufacturing, can solve the problem that the strength and corrosion resistance of the aluminum alloy plate are difficult to meet at the same time, achieve excellent thermal exposure stability and corrosion resistance, improve strength, ensure stability and The effect of corrosion resistance
- Summary
- Abstract
- Description
- Claims
- Application Information
AI Technical Summary
Problems solved by technology
Method used
Examples
Embodiment 1
[0029] Provided is a method for manufacturing a baking-painted aluminum alloy plate. The mass percent content of each component of the aluminum alloy is: Zn 6%, Mg 5%, Cr 1%, Zr 0.8%, Ti 0.7%, Al 0.3%, Ni 0.06%, Fe 0.04%, Si 0.04%, Sc0.05%, Y 0.02%, the balance is aluminum and unavoidable non-metallic inclusions,
[0030] (1) According to the elemental composition, put the component raw materials into the melting furnace for smelting at 770°C. After all the furnace materials are melted, stir for 10 minutes, and then add refining agent for refining. The refining temperature is 760°C, and the refining time is 40 minutes. Set for 60min, pass into Cl 2 , N 2 The mixed gas further treats the impurities in the alloy, and the gas flow rate is 3m 3 / min, stand still for 60min, carry out slag removal; obtain aluminum alloy molten liquid;
[0031] (2) Casting the molten aluminum alloy, controlling the temperature to 720° C., to obtain an aluminum alloy ingot;
[0032] (3) Heat the a...
Embodiment 2
[0040] Provided is a method for manufacturing a baking varnish aluminum alloy plate. The mass percent content of each component of the aluminum alloy is: Zn 8%, Mg 6%, Cr 2%, Zr 0.9%, Ti 0.8%, Al 0.4%, Ni 0.07%, Fe 0.05%, Si 0.05%, Sc0.06%, Y 0.03%, the balance is aluminum and unavoidable non-metallic inclusions,
[0041] (1) According to the elemental composition, put the component raw materials into the melting furnace for smelting at 775°C. After all the furnace materials are melted, stir for 15 minutes, and then add refining agent for refining. The refining temperature is 765°C, and the refining time is 50 minutes. Set for 60min, pass into Cl 2 , N 2 The mixed gas further treats the impurities in the alloy, and the gas flow rate is 4m 3 / min, stand still for 60min, carry out slag removal; obtain aluminum alloy molten liquid;
[0042] (2) Casting the molten aluminum alloy, controlling the temperature to 730° C., to obtain an aluminum alloy ingot;
[0043] (3) Heat the a...
Embodiment 3
[0051] Provided is a method for manufacturing a baking-painted aluminum alloy plate. The mass percent content of each component of the aluminum alloy is: Zn 7%, Mg 5.5%, Cr 1.5%, Zr 0.85%, Ti 0.75%, Al 0.35%, Ni 0.065% , Fe 0.045%, Si0.045%, Sc 0.055%, Y 0.025%, the balance is aluminum and unavoidable non-metallic inclusions,
[0052] (1) According to the elemental composition, put the component raw materials into the melting furnace for smelting at 773°C. After all the furnace materials are melted, stir for 13 minutes, and then add refining agent for refining. The refining temperature is 763°C, and the refining time is 45 minutes. Set for 60min, pass into Cl 2 , N 2 The mixed gas further treats the impurities in the alloy, and the gas flow rate is 3.5m 3 / min, stand still for 60min, carry out slag removal; obtain aluminum alloy molten liquid;
[0053] (2) Casting the molten aluminum alloy, controlling the temperature to 725° C., to obtain an aluminum alloy ingot;
[0054]...
PUM
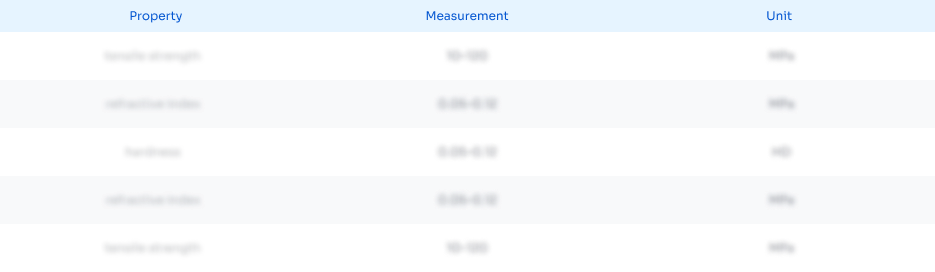
Abstract
Description
Claims
Application Information

- R&D
- Intellectual Property
- Life Sciences
- Materials
- Tech Scout
- Unparalleled Data Quality
- Higher Quality Content
- 60% Fewer Hallucinations
Browse by: Latest US Patents, China's latest patents, Technical Efficacy Thesaurus, Application Domain, Technology Topic, Popular Technical Reports.
© 2025 PatSnap. All rights reserved.Legal|Privacy policy|Modern Slavery Act Transparency Statement|Sitemap|About US| Contact US: help@patsnap.com