Printing ink for various compound processes
A compounding process and ink technology, applied in inks, applications, household appliances, etc., can solve problems such as extrusion compounding and solvent-free compounding, high temperature resistance of ink, and darkening of compound products, etc., to improve penetration, Improve high temperature resistance and reduce volatilization
- Summary
- Abstract
- Description
- Claims
- Application Information
AI Technical Summary
Problems solved by technology
Method used
Image
Examples
Embodiment 1
[0066] 1, at first adopt ethyl acetate, n-propyl acetate to dissolve 20% modified binary, ternary chlorine vinegar resin to prepare 15% modified binary, ternary chlorine vinegar mixed resin liquid, wherein the weight percent of each component is:
[0067]
[0068] 2. Then, according to the following formula system:
[0069] 30% modified polyurethane resin liquid: 25%
[0070] 15% modified binary and ternary chlorine vinegar mixed resin solution: 15%
[0071] Pigment: 10%
[0072] Filler: 3%
[0073] Polyethylene wax: 3%
[0074] Special additives: 5%
[0075] n-Propyl acetate: 13%
[0076] Isopropanol: 10%
[0077] Ethyl acetate: 15%
[0078] Silane coupling agent: 1%
[0079] Wherein the component and weight percent of special auxiliary agent are:
[0080] 2400 hyperdispersant 20%
[0081] Antistatic agent 40%
[0082] Antioxidant 40%
[0083] Wherein the component and weight percent of silane coupling agent are:
[0084] Aminopropyltrimethoxysilane (A~1110) 50%...
Embodiment 2
[0097] 1. The preparation of 15% modified binary and ternary chlorine vinegar mixed resin liquid is the same as in Example 1.
[0098] 2. Then, according to the following formula system:
[0099] 30% modified polyurethane resin liquid: 32%
[0100] 15% modified binary and ternary chlorine vinegar mixed resin solution: 10%
[0101] Pigment: 20%
[0102] Filler: 4%
[0103] Polyethylene wax: 1%
[0104] Special additives: 1%
[0105] n-Propyl acetate: 14%
[0106] Isopropanol: 5%
[0107] Ethyl acetate: 10%
[0108] Silane coupling agent: 3%
[0109] Wherein the component and weight percent of special auxiliary agent are:
[0110] 2400 hyperdispersant 20%
[0111] Antistatic agent 40%
[0112] Antioxidant 40%
[0113] Wherein the component and weight percent of silane coupling agent are:
[0114] Aminopropyltrimethoxysilane (A~1110) 50%
[0115] Vinylethoxysilane (A~151) 35%
[0116] Isobutyltriethoxysilane (TMA) 15%
[0117] The ink used in various composite pro...
Embodiment 3
[0120] 1. The preparation of 15% modified binary and ternary chlorine vinegar mixed resin liquid is the same as in Example 1.
[0121] 2. Then, according to the following formula system:
[0122] 30% modified polyurethane resin liquid: 25%
[0123] 30% modified polyurethane ~ acrylic emulsion: 6%
[0124] 15% modified binary and ternary chlorine vinegar mixed resin solution: 10%
[0125] Pigment: 8%
[0126] Filler: 7%
[0127] Polyethylene wax: 1%
[0128] Special additives: 1.5%
[0129] n-Propyl acetate: 10%
[0130] Isopropanol: 20%
[0131] Ethyl acetate: 10%
[0132] Silane coupling agent: 1.5%
[0133] Wherein the component and weight percent of special auxiliary agent are:
[0134] 2400 hyperdispersant 20%
[0135] Antistatic agent 40%
[0136] Antioxidant 40%
[0137] Wherein the component and weight percent of silane coupling agent are:
[0138] Aminopropyltrimethoxysilane (A~1110) 50%
[0139] Vinylethoxysilane (A~151) 35%
[0140] Isobutyltriethoxys...
PUM
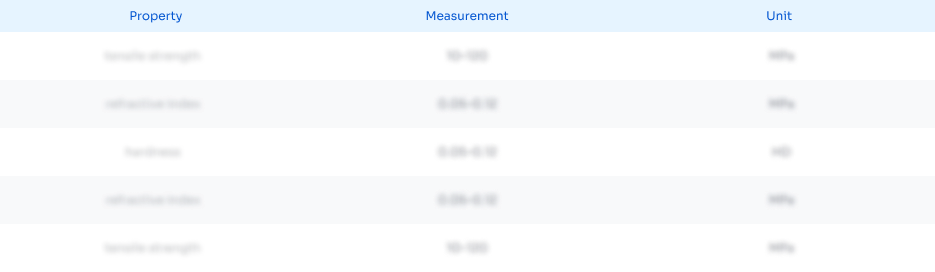
Abstract
Description
Claims
Application Information

- R&D
- Intellectual Property
- Life Sciences
- Materials
- Tech Scout
- Unparalleled Data Quality
- Higher Quality Content
- 60% Fewer Hallucinations
Browse by: Latest US Patents, China's latest patents, Technical Efficacy Thesaurus, Application Domain, Technology Topic, Popular Technical Reports.
© 2025 PatSnap. All rights reserved.Legal|Privacy policy|Modern Slavery Act Transparency Statement|Sitemap|About US| Contact US: help@patsnap.com