Method for achieving vacuum in composite blank assembly welding process
A realization method and a composite billet technology, applied in welding equipment, metal processing, metal processing equipment, etc., can solve the problems of difficulty in maintaining the vacuum state of the joint surface of two slabs and reduce the composite quality of the joint surface, so as to promote dissipation and avoid Welding oxidation, the effect of improving composite quality
- Summary
- Abstract
- Description
- Claims
- Application Information
AI Technical Summary
Problems solved by technology
Method used
Image
Examples
Embodiment Construction
[0028] see figure 1 , a method for realizing vacuum during welding of a composite billet assembly of the present invention, comprising the steps of:
[0029] 1) Backup board
[0030] Take two slabs 1 and 2, clean the iron oxide scale on the surface of the slabs, and process chamfers around the joint surface A of the slabs to form a groove 3, and then place the cleaned surfaces of the two slabs 1 and 2 face to face in the air;
[0031] 2) Closed welding in the early stage
[0032] Weld two slabs 1 and 2 groove 3, welding at least three layers, each layer thickness 3mm-10mm, to ensure the airtightness of the surrounding welds; during this period, reserve an access hole in the weld;
[0033] 3) Vacuum extraction
[0034] Use a mechanical vacuum pump to enter the access hole reserved for the weld to draw a vacuum between the two slabs, and draw the vacuum to below 10Pa, and then use a molecular vacuum pump to continue to draw the vacuum to below 0.01Pa;
[0035] 4) Two-step w...
PUM
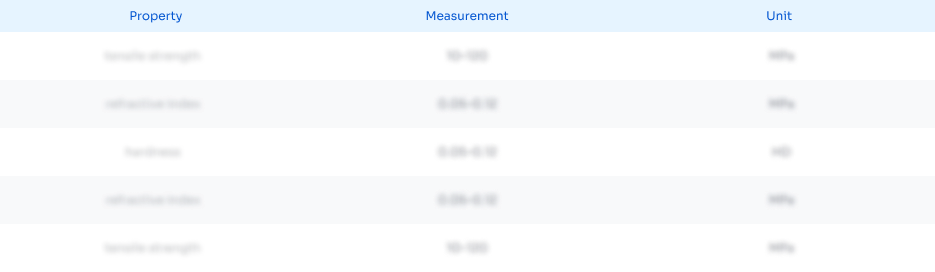
Abstract
Description
Claims
Application Information

- R&D Engineer
- R&D Manager
- IP Professional
- Industry Leading Data Capabilities
- Powerful AI technology
- Patent DNA Extraction
Browse by: Latest US Patents, China's latest patents, Technical Efficacy Thesaurus, Application Domain, Technology Topic, Popular Technical Reports.
© 2024 PatSnap. All rights reserved.Legal|Privacy policy|Modern Slavery Act Transparency Statement|Sitemap|About US| Contact US: help@patsnap.com