Method for measuring coating thickness and interfacial roughness simultaneously by ultrasonic
A coating and ultrasonic technology, which is applied in the direction of using ultrasonic/sonic/infrasonic waves, measuring devices, instruments, etc., can solve the problems of difficulty in characterizing thickness and roughness, inappropriate for coating layer and substrate interface roughness measurement, etc.
- Summary
- Abstract
- Description
- Claims
- Application Information
AI Technical Summary
Problems solved by technology
Method used
Image
Examples
Embodiment Construction
[0029] A method for simultaneously measuring the thickness of the coating layer and the roughness of the internal interface by ultrasonic waves, using figure 2 The one shown includes a sample table (1), a rough coating layer sample on the inner interface (prepared by shot blasting on the surface of a Ni-based superalloy, the thickness of the thin layer is about 0.5-0.7 mm, and the nominal roughness values are 8 μm and 14 μm respectively. With 3 tested samples of 28μm, the back of the sample is ground flat with 2000# sandpaper, and polished to eliminate the influence of back fluctuations) (2), the nominal frequency is 20MHz delay block probe, and the chip diameter is 6mm (3) , USIP40 flaw detector (4), DPO4O32 digital oscilloscope (5) and ultrasonic pulse echo detection system of computer (6);
[0030] It uses the following measurement steps:
[0031](1) Connect the delay block probe to the system and calibrate the instrument. The reflected sound pressure of the delay bloc...
PUM
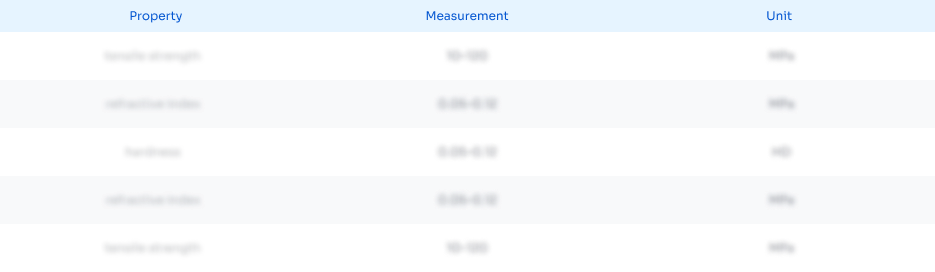
Abstract
Description
Claims
Application Information

- Generate Ideas
- Intellectual Property
- Life Sciences
- Materials
- Tech Scout
- Unparalleled Data Quality
- Higher Quality Content
- 60% Fewer Hallucinations
Browse by: Latest US Patents, China's latest patents, Technical Efficacy Thesaurus, Application Domain, Technology Topic, Popular Technical Reports.
© 2025 PatSnap. All rights reserved.Legal|Privacy policy|Modern Slavery Act Transparency Statement|Sitemap|About US| Contact US: help@patsnap.com