A kind of cyanidation tailing residue waste residue degradation treatment process
A treatment process and a technology for cyanidation tailings, which are applied in the field of degradation treatment technology of cyanidation tailings and waste residues, can solve the problems of poor mass transfer between cyanide tailings and oxidants, overcome harsh pressure requirements, and accelerate hydrolysis and oxidation processes. , the effect of process safety
- Summary
- Abstract
- Description
- Claims
- Application Information
AI Technical Summary
Problems solved by technology
Method used
Examples
Embodiment 1
[0036] Put the cyanide tailings containing cuprous thiocyanide into the rotary drum autoclave, vacuumize for half an hour after sealing, keep the vacuum at minus 0.09MPa, and then empty it. After emptying, feed water steam into the rotary drum autoclave, adjust the rotation speed of the autoclave to 30 rpm, adjust the water vapor pressure to keep the temperature at 140°C and start curing. After 3 hours of constant pressure curing, adjust the steam The pressure is about 0.2MPa, so that the temperature in the autoclave is kept at 120-130°C (the pressure is only for the convenience of adjusting and indicating, and the temperature in the autoclave shall prevail). Then feed ozone into the air inlet of the autoclave (ozone comes from an ozone generator), adjust the pressure of the ozone to maintain balance with the pressure in the autoclave, connect the gas outlet of the autoclave to an ozone destroyer, and keep the pressure for 1 hour. After oxidation, adjust the rotation speed of ...
Embodiment 2
[0038] Put the cyanidation tailings containing Prussian blue into the rotary drum autoclave, seal it and then vacuum it for half an hour, keep the vacuum at minus 0.06MPa, and then empty it. After emptying, feed water steam into the rotary drum autoclave, adjust the rotation speed of the autoclave to 40 rpm, adjust the water vapor pressure to keep the temperature at 150°C and start curing. After 4 hours of constant pressure curing, adjust the steam The pressure is about 0.2MPa, so that the temperature in the autoclave is kept at 120-130°C (the pressure is only used as an auxiliary indicator for adjusting the temperature, and the temperature in the autoclave shall prevail). Then pass ozone into the air inlet of the autoclave (ozone comes from the ozone steel cylinder), adjust the pressure of the ozone to maintain balance with the pressure in the autoclave, connect the gas outlet of the autoclave to an ozone destroyer, and keep the pressure for 2 hours. After oxidation, adjust t...
PUM
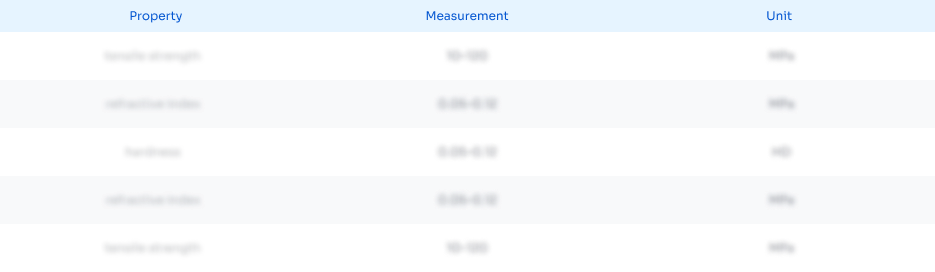
Abstract
Description
Claims
Application Information

- R&D
- Intellectual Property
- Life Sciences
- Materials
- Tech Scout
- Unparalleled Data Quality
- Higher Quality Content
- 60% Fewer Hallucinations
Browse by: Latest US Patents, China's latest patents, Technical Efficacy Thesaurus, Application Domain, Technology Topic, Popular Technical Reports.
© 2025 PatSnap. All rights reserved.Legal|Privacy policy|Modern Slavery Act Transparency Statement|Sitemap|About US| Contact US: help@patsnap.com