Method for preparing chlorine-removal alkali residue mixture by utilizing alkali residues through ammonia-soda process and application of chlorine-removal alkali residue mixture
A technology of mixture and ammonia-alkali method, applied in separation methods, chemical instruments and methods, solid waste removal, etc., can solve the problems of low utilization value, decreased utilization rate, consumption, etc., achieve good chlorine removal effect and reduce chloride ions The effect of content
- Summary
- Abstract
- Description
- Claims
- Application Information
AI Technical Summary
Problems solved by technology
Method used
Examples
Embodiment 1
[0030] A method for preparing the chlorine-alkali slag mixture by using the ammonia-soda method alkali slag, comprising the steps of:
[0031] Step 1, first crush and grind the returned sand and stone back into sand and back stone powder;
[0032] Step 2. Soak the sand-returning-stone powder in water for 0.5 days to digest the burnt calcium oxide. While soaking the sand-returning-stone powder, stir intermittently, then mix the digested sand-returning-stone powder, alkali slag, and water, and use the material In terms of mass percentage, the ratio of the digested sand-returning stone powder and alkali slag is 2:8, and the total mass of water is 8 times the total mass of the digested sand-returning stone powder and alkali slag;
[0033] Step 3, performing pressure filtration treatment to obtain a chlorine-alkali removal slag mixture with a chloride ion content of 0.28% of the total solid mass in the mixture.
[0034] In this embodiment, one or more of fly ash, limestone powder,...
Embodiment 2
[0037] A method for preparing the chlorine-alkali slag mixture by using the ammonia-soda method alkali slag, comprising the steps of:
[0038] Step 1, first crush and grind the returned sand and stone back into sand and back stone powder;
[0039] Step 2. Soak the sand-returning-stone powder in water for 3 days to digest the burnt calcium oxide. While soaking the sand-returning-stone powder, stir intermittently, then mix the digested sand-returning-stone powder, alkali slag, and water, and use the material In terms of mass percentage, the ratio of the digested sand-returning stone powder and alkali slag is 3:7, and the total mass of water is 7 times the total mass of the digested sand-returning stone powder and alkali slag;
[0040] Step 3, performing pressure filtration treatment to obtain a chlorine-alkali removal slag mixture with a chloride ion content of 0.08% of the total solid mass in the mixture.
[0041] In this embodiment, one or more of fly ash, limestone powder, s...
Embodiment 3
[0044] A method for preparing the chlorine-alkali slag mixture by using the ammonia-soda method alkali slag, comprising the steps of:
[0045] Step 1, first crush and grind the returned sand and stone back into sand and back stone powder;
[0046] Step 2. Soak the sand-returning stone powder in water for 7 days to digest the burnt calcium oxide. While soaking the sand-returning stone powder, stir intermittently, then mix the digested sand-returning stone powder, alkali slag, and water, and use the material In terms of mass percentage, the ratio of the digested sand-returning stone powder and alkali slag is 5:5, and the total mass of water is 3 times the total mass of the digested sand-returning stone powder and alkali slag;
[0047] Step 3, performing pressure filtration treatment to obtain a chlorine-alkali removal slag mixture with a chloride ion content of 0.05% of the total mass of solids in the mixture.
[0048] In this embodiment, one or more of fly ash, limestone powde...
PUM
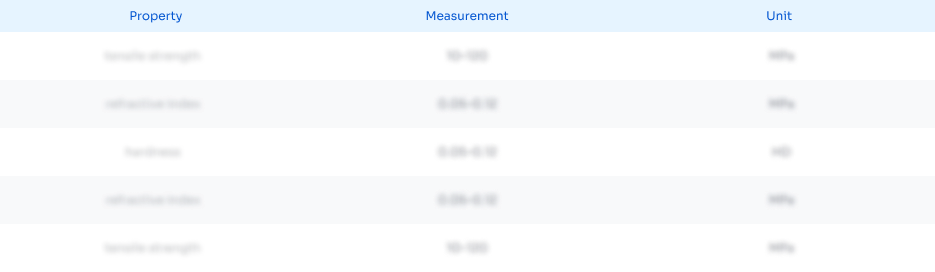
Abstract
Description
Claims
Application Information

- Generate Ideas
- Intellectual Property
- Life Sciences
- Materials
- Tech Scout
- Unparalleled Data Quality
- Higher Quality Content
- 60% Fewer Hallucinations
Browse by: Latest US Patents, China's latest patents, Technical Efficacy Thesaurus, Application Domain, Technology Topic, Popular Technical Reports.
© 2025 PatSnap. All rights reserved.Legal|Privacy policy|Modern Slavery Act Transparency Statement|Sitemap|About US| Contact US: help@patsnap.com