Electroslag casting production method for waterwheel blade green compact
An electroslag casting and manufacturing method technology, which is applied in the field of three-dimensional curved surface green compact manufacturing technology, can solve the problems that restrict the development of hydraulic turbine blade thermal molding technology, the heavy workload of welding repair and relief grinding correction of casting compact, and the inherent quality of casting compact Low-level problems, to achieve the effects of saving production costs and time, small deformation, and large crystallization temperature gradient
- Summary
- Abstract
- Description
- Claims
- Application Information
AI Technical Summary
Problems solved by technology
Method used
Examples
Embodiment 1
[0021] Martensitic stainless steel blades made of 06Cr13Ni5Mo were selected to prepare electroslag casting blade compacts.
[0022] (1) Use the finite element analysis software to carry out three-dimensional intelligent development of the turbine blades, and develop the turbine blades into a blade molded compact with a flat front and a curved back, and determine the outer contour size of the blade compact. The length is about 350mm and the maximum width The thickness is 220mm, the maximum thickness is 65mm, and the minimum thickness is 13mm.
[0023] (2) The choice of crystallizer, copper-steel welded split combined crystallizer, and the crystallizer can be disassembled separately, the inner cavity of the crystallizer is copper plate, the water joint between the inner cavity plate and the rib plate of the copper-steel welded crystallizer The width is 33mm, and the copper plate in the cavity of the crystallizer is prepared by metal hot bending + machining manufacturing process....
Embodiment 2
[0047] Martensitic stainless steel blades made of 06Cr13Ni4Mo were selected to prepare electroslag casting blade compacts.
[0048] (1) Use the finite element analysis software to carry out three-dimensional intelligent expansion of the turbine blades, and develop the turbine blades into a blade molded compact with a flat front and a curved back, and determine the outer contour size of the blade compact. The length is about 500mm and the maximum width 300mm, the maximum thickness is 80mm, and the minimum thickness is 15mm.
[0049] (2) The choice of crystallizer, copper-steel welded split combined mold, and the crystallizer can be disassembled separately, the width of the water joint between the inner cavity plate and the rib plate of the copper-steel welded crystallizer is 20mm, and the copper plate in the inner cavity of the mold Prepared for metal hot bending + machining manufacturing process.
[0050] (3) Combined with the size of the inner cavity of the blade compact cry...
Embodiment 3
[0060] Martensitic stainless steel blades made of 06Cr16Ni5Mo were selected to prepare electroslag casting X-shaped blade compacts.
[0061] (1) According to the three-dimensional intelligent development size of the turbine blade, determine the outer contour size of the blade compact. The blade length is about 800mm, the maximum width is 500mm, the maximum thickness is 150mm, and the minimum thickness is 30mm.
[0062] (2) The choice of crystallizer, all-aluminum alloy split combined mold, and the crystallizer can be disassembled separately, the width of the water joint between the inner cavity plate and the rib plate of the mold is 30mm, and the inner cavity of the mold is prepared by casting forming method
[0063] (3) Combined with the size of the inner cavity of the blade compact crystallizer, the blade compact conformal consumable electrode was prepared, the filling ratio was selected as 0.41, and the prepared consumable electrode was a steel plate tailor welding electrode...
PUM
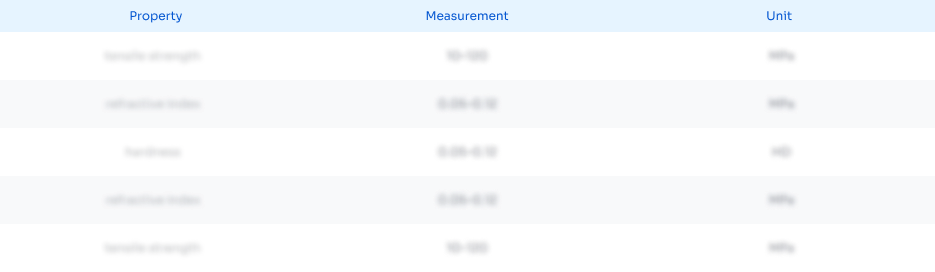
Abstract
Description
Claims
Application Information

- R&D
- Intellectual Property
- Life Sciences
- Materials
- Tech Scout
- Unparalleled Data Quality
- Higher Quality Content
- 60% Fewer Hallucinations
Browse by: Latest US Patents, China's latest patents, Technical Efficacy Thesaurus, Application Domain, Technology Topic, Popular Technical Reports.
© 2025 PatSnap. All rights reserved.Legal|Privacy policy|Modern Slavery Act Transparency Statement|Sitemap|About US| Contact US: help@patsnap.com