Method for smelting ferro-molybdenum from ammonia leaching residue to recover molybdenum
An ammonia leaching and ferromolybdenum technology is applied in the field of molybdenum metallurgy, which can solve the problems of unstable technical and economic indicators and treatment results, severe acid corrosion, and high equipment investment, so as to improve the comprehensive utilization process, efficient recycling, and metal recovery. high rate effect
- Summary
- Abstract
- Description
- Claims
- Application Information
AI Technical Summary
Problems solved by technology
Method used
Image
Examples
Embodiment 1
[0023] The method for recovering molybdenum by smelting ferromolybdenum from ammonia leaching residue in this embodiment includes the following steps:
[0024] Step 1. Add 1000kg of ammonia leaching residue and auxiliary materials into the blender and mix uniformly to obtain a mixed material; the auxiliary material is composed of 293kg ferrosilicon, 346kg iron phosphorus, 69kg aluminum particles, 223kg sodium nitrate and 60kg calcium oxide; The mass percentage of molybdenum in the leaching slag is 18%, and the average particle size of the ammonia leaching slag is not greater than 5mm; the mass percentage of silicon in the ferrosilicon is 75%, and the mass percentage of iron in iron and phosphorus is 67%. The mass percentage of aluminum in the aluminum particles is 98%, the mass purity of sodium nitrate is 98%, and the mass purity of calcium oxide is 85%;
[0025] Step 2. Put the mixture described in step 1 into the smelting furnace, cover the surface of the mixture with a layer of ...
Embodiment 2
[0030] The method for recovering molybdenum by smelting ferromolybdenum from ammonia leaching residue in this embodiment includes the following steps:
[0031] Step 1. Add 1000kg of ammonia leaching residue and auxiliary materials into the blender and mix uniformly to obtain a mixed material; the auxiliary material is composed of 280kg ferrosilicon, 360kg iron phosphorus, 50kg aluminum particles, 180kg sodium nitrate and 80kg calcium oxide; The mass percentage of molybdenum in the leaching slag is 10%, and the average particle size of the ammonia leaching slag is not more than 5mm; the mass percentage of silicon in the ferrosilicon is 76%, and the mass percentage of iron in iron and phosphorus is 68%. The mass percentage of aluminum in the aluminum particles is 98%, the mass purity of sodium nitrate is 95%, and the mass purity of calcium oxide is 90%;
[0032] Step 2. Put the mixture described in step one into the smelting furnace, cover the surface of the mixture with a layer of i...
Embodiment 3
[0037] The method for recovering molybdenum by smelting ferromolybdenum from ammonia leaching residue in this embodiment includes the following steps:
[0038] Step 1. Add 1000kg of ammonia leaching residue and auxiliary materials into the mixer and mix uniformly to obtain a mixture material; the auxiliary material is composed of 310kg ferrosilicon, 290kg iron phosphorus, 80kg aluminum particles, 260kg sodium nitrate and 55kg fluorite; The mass percentage of molybdenum in the leaching slag is 20%, and the average particle size of the ammonia leaching slag is not more than 5mm; the mass percentage of silicon in the ferrosilicon is 72%, and the mass percentage of iron in iron and phosphorus is 64%. The mass percentage of aluminum in the aluminum particles is 95%, the mass purity of sodium nitrate is 96%, and the mass percentage of calcium fluoride in fluorite is 90%;
[0039] Step 2. Put the mixture described in step one into the smelting furnace, cover the surface of the mixture wit...
PUM
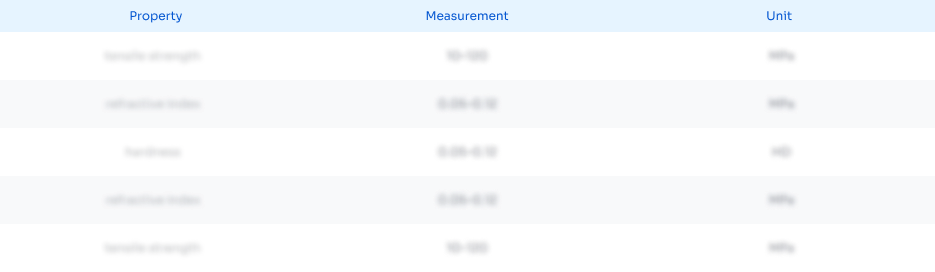
Abstract
Description
Claims
Application Information

- R&D Engineer
- R&D Manager
- IP Professional
- Industry Leading Data Capabilities
- Powerful AI technology
- Patent DNA Extraction
Browse by: Latest US Patents, China's latest patents, Technical Efficacy Thesaurus, Application Domain, Technology Topic, Popular Technical Reports.
© 2024 PatSnap. All rights reserved.Legal|Privacy policy|Modern Slavery Act Transparency Statement|Sitemap|About US| Contact US: help@patsnap.com