Synthetic brake shoe for high-power locomotive pressed at room temperature and preparation method thereof
A technology of pressing and synthesizing brake shoes at room temperature, applied in the field of brake pad materials, can solve the problems of metal inlay, easy fracture of friction body, etc., achieve the effect of low equipment and mold requirements, solve thermal recession, and reduce labor costs
- Summary
- Abstract
- Description
- Claims
- Application Information
AI Technical Summary
Problems solved by technology
Method used
Image
Examples
Embodiment Construction
[0015] The present invention will be further described in detail below in combination with specific embodiments.
[0016] 1. The composite brake shoe for a high-power locomotive provided by the present invention includes a steel back and a brake shoe body, and the brake shoe body is fixed on the steel back. The brake shoe body is synthesized by the following volume ratio of each component material (see the following table for the formula of the embodiment, which is not used to limit the present invention).
[0017]
[0018] The raw materials used in the present invention are industrial-grade conventional products, all of which are commercially available.
[0019] The formula design of the invention is scientific and reasonable, and the synthetic brake shoe can better meet various performance indexes required in domestic and international rail transit industry standards. The formula brake shoe can be used in high-power locomotives with a maximum operating speed of 120km / h a...
PUM
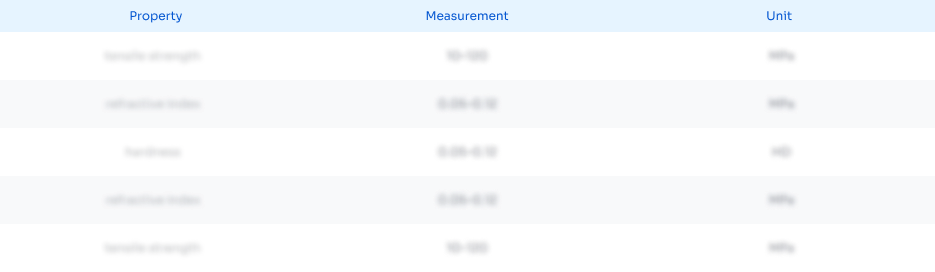
Abstract
Description
Claims
Application Information

- R&D
- Intellectual Property
- Life Sciences
- Materials
- Tech Scout
- Unparalleled Data Quality
- Higher Quality Content
- 60% Fewer Hallucinations
Browse by: Latest US Patents, China's latest patents, Technical Efficacy Thesaurus, Application Domain, Technology Topic, Popular Technical Reports.
© 2025 PatSnap. All rights reserved.Legal|Privacy policy|Modern Slavery Act Transparency Statement|Sitemap|About US| Contact US: help@patsnap.com