Precise cold forging formed cam sheet manufacturing method
A manufacturing method and technology of cam sheets, which are applied in mechanical equipment, engine components, metal processing equipment, etc., can solve the problems of harsh operating environment, complex equipment and large deformation of warm forging, and improve fatigue strength and stress corrosion resistance. capacity, reduced equipment investment and parts costs, the effect of reduced average stress levels
- Summary
- Abstract
- Description
- Claims
- Application Information
AI Technical Summary
Problems solved by technology
Method used
Image
Examples
Embodiment 1
[0056] Such as Figure 5 As shown, the cam piece is made of high-carbon bearing steel or combined steel wire or bar steel after annealing, drawing and lubrication to make it suitable for cold forging; See Figure 5 ) to extrude the final profile of the cam piece; then the forging is subjected to stress annealing (or spheroidizing annealing); finally, it undergoes another extrusion shaping to meet the final size requirements.
[0057] A method for manufacturing a precision cold forging cam plate, comprising the following steps:
[0058] A. Pretreatment step, the wire or bar steel is annealed, drawn and lubricated to make it suitable for the first blank formed by cold heading;
[0059] B. Cold forging forming step, using a horizontal or vertical forging press to forge the cam piece;
[0060] C. Heat treatment;
[0061] Wherein, the cold forging forming step includes an expanding extrusion process.
[0062] Optimally, the cold forging forming step consists of the following o...
Embodiment 2
[0073] The utility model relates to an extrusion punch used in the manufacturing method of a precision cold forging cam sheet, and its front end is a tapered head.
[0074] Optimally, both ends of the extrusion punch are tapered, the diameter of the bottom surface of the tapered head is smaller than the diameter of the through hole in the middle of the cam plate, and the diameter of the bottom surface of the tapered bottom is consistent with the diameter of the through hole in the middle of the cam plate.
PUM
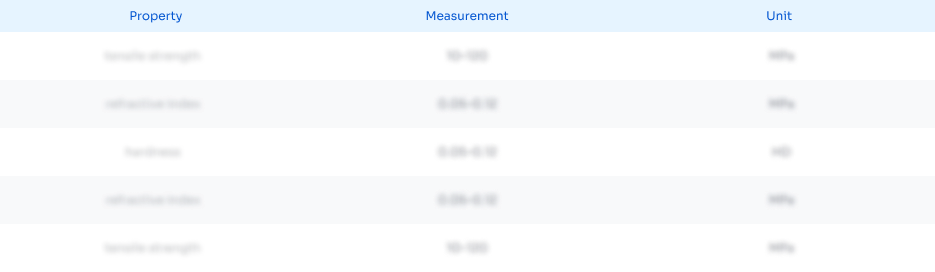
Abstract
Description
Claims
Application Information

- Generate Ideas
- Intellectual Property
- Life Sciences
- Materials
- Tech Scout
- Unparalleled Data Quality
- Higher Quality Content
- 60% Fewer Hallucinations
Browse by: Latest US Patents, China's latest patents, Technical Efficacy Thesaurus, Application Domain, Technology Topic, Popular Technical Reports.
© 2025 PatSnap. All rights reserved.Legal|Privacy policy|Modern Slavery Act Transparency Statement|Sitemap|About US| Contact US: help@patsnap.com