Chip flattening method
A planarization method and chip technology, which is applied in the direction of grinding devices, electrical components, grinding machine tools, etc., can solve the problems of difficulty in controlling the planarization of the chip surface, dish-shaped depressions of silicon wafers, and the reduction of global planarization of the surface of silicon wafers, etc. , to achieve the effect of improving global planarization, improving yield rate, and improving chip surface planarization
- Summary
- Abstract
- Description
- Claims
- Application Information
AI Technical Summary
Problems solved by technology
Method used
Image
Examples
Embodiment Construction
[0020] In order to describe the technical content, achieved goals and effects of the present invention in detail, the following will be described in detail in conjunction with the embodiments and accompanying drawings.
[0021] see figure 1 and Figures 2A-2C , discloses an embodiment of the chip planarization method according to the present invention. In this embodiment, the chip planarization method includes the following steps:
[0022] S110: providing a silicon substrate 11, a metal layer 14 is formed on the silicon substrate 11, the metal layer 14 has an initial thickness, and the initial thickness is 6000-10000 angstroms;
[0023] S120: Grinding the metal layer 14 from an initial thickness to a first target thickness by using a chemical mechanical polishing process with a first down force and a first rotational speed of the turntable. Wherein, the first downforce is set at 1.8-2.3 psi, the first turntable speed is set at 70-150 rpm, and the first target thickness is 1...
PUM
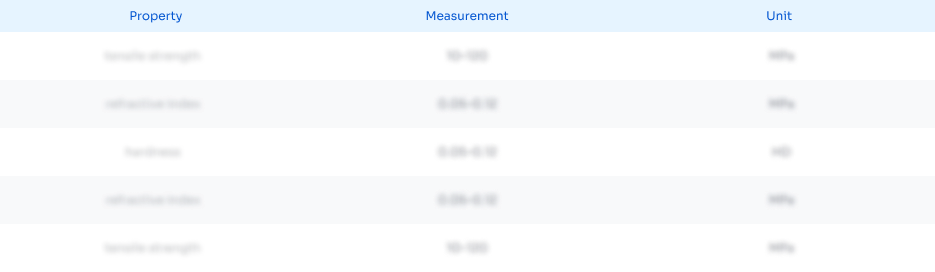
Abstract
Description
Claims
Application Information

- R&D Engineer
- R&D Manager
- IP Professional
- Industry Leading Data Capabilities
- Powerful AI technology
- Patent DNA Extraction
Browse by: Latest US Patents, China's latest patents, Technical Efficacy Thesaurus, Application Domain, Technology Topic, Popular Technical Reports.
© 2024 PatSnap. All rights reserved.Legal|Privacy policy|Modern Slavery Act Transparency Statement|Sitemap|About US| Contact US: help@patsnap.com