Circulating process for producing propylene oxide by using chlorohydrination method
A technology of propylene oxide and chlorohydrin, applied in organic chemistry and other directions, can solve the problems of high energy consumption and no economic feasibility, and achieve the effects of reducing consumption, reducing evaporation cost and improving utilization rate
- Summary
- Abstract
- Description
- Claims
- Application Information
AI Technical Summary
Problems solved by technology
Method used
Examples
Embodiment 1
[0049] A kind of chloroalcoholization method produces the recycling process of propylene oxide, comprises the following steps:
[0050] (1) Add hydrochloric acid to adjust the pH to 6.8 in the saline wastewater (brine containing 5% calcium chloride by mass fraction) produced in the chlorohydrination reactor, and then hydrogen peroxide or ozone is introduced to remove the saline wastewater Medium organic matter;
[0051] (2) The wastewater treated in step (1) enters the MVR evaporator for evaporation and concentration, and the separated steam is compressed by the turbo compressor, the temperature and pressure increase, and the heat enthalpy increases, and then returns to the MVR evaporator for recycling; the condensate Enter the biochemical treatment system for treatment. The treated wastewater is filtered and sterilized and then enters the circulating water system for use. The concentrated wastewater is filtered by the ceramic membrane and then enters the diaphragm electrolyze...
Embodiment 2
[0056] A kind of chloroalcoholization method produces the recycling process of propylene oxide, comprises the following steps:
[0057] (1) Add hydrochloric acid to adjust the pH to 7.5 in the saline waste water (comprising the brine of 4% sodium chloride by mass fraction) produced in the chloroalcoholization reactor, and then hydrogen peroxide or pass into ozone to remove the saline waste water Medium organic matter;
[0058] (2) The wastewater treated in step (1) enters the MVR evaporator for evaporation and concentration, and the separated steam is compressed by the turbo compressor, the temperature and pressure increase, and the heat enthalpy increases, and then returns to the MVR evaporator for recycling; the condensate Enter the biochemical treatment system for treatment. The treated wastewater is filtered and sterilized and then enters the circulating water system for use. The concentrated wastewater is filtered by the ceramic membrane and then enters the diaphragm elec...
PUM
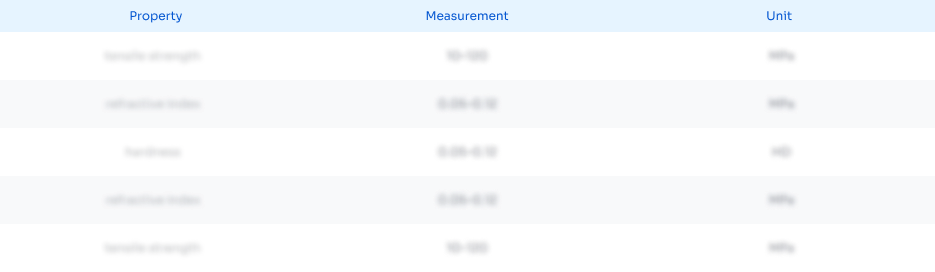
Abstract
Description
Claims
Application Information

- Generate Ideas
- Intellectual Property
- Life Sciences
- Materials
- Tech Scout
- Unparalleled Data Quality
- Higher Quality Content
- 60% Fewer Hallucinations
Browse by: Latest US Patents, China's latest patents, Technical Efficacy Thesaurus, Application Domain, Technology Topic, Popular Technical Reports.
© 2025 PatSnap. All rights reserved.Legal|Privacy policy|Modern Slavery Act Transparency Statement|Sitemap|About US| Contact US: help@patsnap.com