Calcium carbide cooling molding device
A cooling forming, calcium carbide technology, applied in sustainable manufacturing/processing, carbide, chemical industry, etc., can solve problems such as high power consumption, increased calcium carbide cost, long cooling time, etc., to reduce energy loss and reduce calcium carbide powder Or the production of electric lime, the effect of simplifying the production process
- Summary
- Abstract
- Description
- Claims
- Application Information
AI Technical Summary
Problems solved by technology
Method used
Image
Examples
Embodiment Construction
[0022] The present invention provides a kind of calcium carbide cooling molding equipment, see figure 1 , a container 1 with an open upper part is provided, and the container includes a horizontal sieve plate 3 and a cylindrical side wall wrapped around the outside of the sieve plate, and the sieve plate is provided with a number of sieve holes 4 penetrating up and down. The opening of the part of the side wall above the sieve plate is formed as a calcium carbide injection port, the side wall is provided with a hoisting structure and feet, the lower opening of the side wall or the side wall is located on the The bottom of the sieve plate is provided with a movable gate 2 that can be opened and closed, such as a horizontally drawn movable gate. When in use, the calcium carbide that is about to change from a molten state to a solid phase is injected into the container, and the molten calcium carbide temporarily stays on the sieve plate in the container, and after passing throug...
PUM
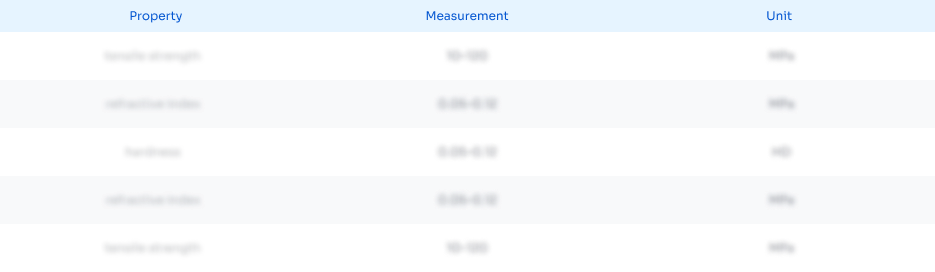
Abstract
Description
Claims
Application Information

- R&D Engineer
- R&D Manager
- IP Professional
- Industry Leading Data Capabilities
- Powerful AI technology
- Patent DNA Extraction
Browse by: Latest US Patents, China's latest patents, Technical Efficacy Thesaurus, Application Domain, Technology Topic, Popular Technical Reports.
© 2024 PatSnap. All rights reserved.Legal|Privacy policy|Modern Slavery Act Transparency Statement|Sitemap|About US| Contact US: help@patsnap.com