Treatment method for improving performance of 3D printing metal workpiece
A technology of 3D printing and processing method is applied in the field of processing to improve the performance of 3D printed metal parts to achieve the effects of improving performance, enhancing wear resistance and increasing stability
- Summary
- Abstract
- Description
- Claims
- Application Information
AI Technical Summary
Problems solved by technology
Method used
Examples
Embodiment 1
[0022] Put the 3D-printed metal sheet using aluminum alloy powder into a cryogenic treatment device, and cool it down from room temperature to -190°C at 2°C / min and keep the temperature constant for 10h.
[0023] After the metal parts that have been subjected to cryogenic treatment once are heated to room temperature at 5°C / min, after a time interval of 20min, they are heated to 200°C for tempering treatment and kept for 2h.
[0024] Finally, place the metal piece in the air and let it cool down to room temperature naturally.
[0025] Put the above-mentioned metal parts cooled to room temperature into the cryogenic treatment device again, and lower the temperature from room temperature to -160 °C at 5 °C / min and keep the temperature constant for 10 h.
[0026] After the second cryogenically treated metal piece is heated to room temperature at 10°C / min, after a time interval of 20min, it is heated to 180°C for tempering treatment and kept for 3h.
[0027] Finally, the metal pa...
Embodiment 2
[0030] Put the 3D-printed metal cylinder using tool steel powder into the cryogenic treatment device, and cool it from room temperature to -190°C at 1°C / min and keep the temperature constant for 15h.
[0031] Raise the temperature of the metal parts that have been cryogenically treated once to room temperature at 3°C / min, and after a time interval of 15 minutes, heat to 180°C for tempering treatment and keep warm for 5h.
[0032] Finally, place the metal piece in the air and let it cool down to room temperature naturally.
[0033] Put the above-mentioned metal parts cooled to room temperature into the cryogenic treatment device again, and lower the temperature from room temperature to -180 °C at 10 °C / min and keep the temperature constant for 12 hours.
[0034] The metal parts subjected to secondary cryogenic treatment were raised to room temperature at 14°C / min, and after a time interval of 15 minutes, heated to 200°C for tempering treatment and kept for 4 hours.
[0035] Fi...
Embodiment 3
[0038] Put the thicker metal plate 3D printed with stainless steel powder into the cryogenic treatment device, cool it from room temperature to -200°C at 5°C / min and keep the temperature constant for 20h.
[0039] Raise the temperature of the metal parts that have been cryogenically treated once to room temperature at 8°C / min, and after a time interval of 10 minutes, heat to 200°C for tempering treatment and keep warm for 5h.
[0040] Finally, place the metal piece in the air and let it cool down to room temperature naturally.
[0041] Put the above-mentioned metal parts into the cryogenic treatment device after cooling to room temperature, and lower the temperature from room temperature to -200 °C at 12 °C / min and keep the temperature constant for 20 hours.
[0042] Raise the temperature of the metal parts subjected to secondary cryogenic treatment to room temperature at 20°C / min, and after a time interval of 10 minutes, heat to 195°C for tempering treatment and keep warm for...
PUM
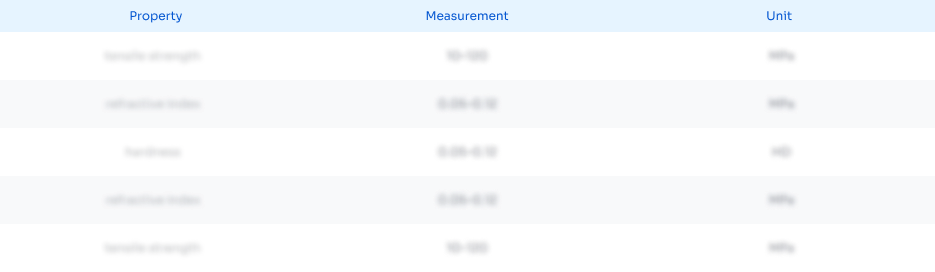
Abstract
Description
Claims
Application Information

- R&D
- Intellectual Property
- Life Sciences
- Materials
- Tech Scout
- Unparalleled Data Quality
- Higher Quality Content
- 60% Fewer Hallucinations
Browse by: Latest US Patents, China's latest patents, Technical Efficacy Thesaurus, Application Domain, Technology Topic, Popular Technical Reports.
© 2025 PatSnap. All rights reserved.Legal|Privacy policy|Modern Slavery Act Transparency Statement|Sitemap|About US| Contact US: help@patsnap.com