Preparation method of copper-graphene complex phase
A technology of graphene and graphene nanosheets, applied in electrolytic coatings, coatings, etc., can solve the problems of poor process controllability, high oxygen content of copper-graphene composite phase, low composite phase resistivity, etc., and achieve mechanical properties And good corrosion resistance, wide application range, avoid the effect of reduction process
- Summary
- Abstract
- Description
- Claims
- Application Information
AI Technical Summary
Problems solved by technology
Method used
Examples
Embodiment 1
[0017] 1) Substrate treatment: Use hydrochloric acid with a molar concentration of 5% to remove oxides on the surface of the copper plate, and then rinse with deionized water;
[0018] 2) Copper plating solution configuration: Dissolve copper sulfate in water, add sulfuric acid, sodium dodecylbenzenesulfonate and hydrochloric acid in sequence, and stir evenly to obtain a copper plating solution; the copper sulfate in the copper plating solution is 200g / L, The sulfuric acid is 80 g / L, the chloride ion is 80 ppm, and the sodium dodecylbenzenesulfonate is 0.1 g / L;
[0019] 3) Electroplating solution configuration: Wet the single-layer graphene nanosheets with a small amount of the copper plating solution prepared in step 2) and ultrasonically, and then add it to the remaining copper plating solution. The concentration of graphene nanosheets is 0.01g / L , fully stirred to obtain a graphene-containing electroplating solution;
[0020] 4) Electroplating: Use the phosphor copper shee...
Embodiment 2
[0022] 1) Substrate treatment: Use hydrochloric acid with a molar concentration of 30% to remove oxides on the surface of the aluminum plate, and then rinse with deionized water;
[0023] 2) Copper plating solution configuration: Dissolve copper sulfate in water, add sulfuric acid, sodium dodecylbenzenesulfonate and hydrochloric acid in sequence, and stir evenly to obtain a copper plating solution; the copper sulfate in the copper plating solution is 150g / L, Sulfuric acid is 90 g / L, chloride ion is 50 ppm, sodium dodecylbenzenesulfonate is 2g / L;
[0024] 3) Electroplating solution configuration: first wet the multilayer graphene nanosheets with a small amount of the copper plating solution configured in step 2) and ultrasonically, and then add it to the remaining copper plating solution. The concentration of the graphene nanosheets is 4g / L. Stir fully to obtain a graphene-containing electroplating solution;
[0025] 4) Electroplating: Use the phosphor copper sheet as the anod...
Embodiment 3
[0027] 1) Substrate treatment: Use hydrochloric acid with a molar concentration of 20% to remove oxides on the surface of the copper tube, and then rinse with deionized water;
[0028] 2) Copper plating solution configuration: Dissolve copper sulfate in water, add sulfuric acid, sodium dodecylbenzenesulfonate and hydrochloric acid in sequence, and stir evenly to obtain a copper plating solution; the copper sulfate in the copper plating solution is 150g / L, The sulfuric acid is 40 g / L, the chloride ion is 50 ppm, and the sodium dodecylbenzenesulfonate is 1 g / L;
[0029] 3) Electroplating solution configuration: Wet the single-layer graphene nanosheets with a small amount of the copper plating solution prepared in step 2) and ultrasonically, and then add it to the remaining copper plating solution. The concentration of graphene nanosheets is 0.1g / L , fully stirred to obtain a graphene-containing electroplating solution;
[0030] 4) Electroplating: use the phosphor copper sheet a...
PUM
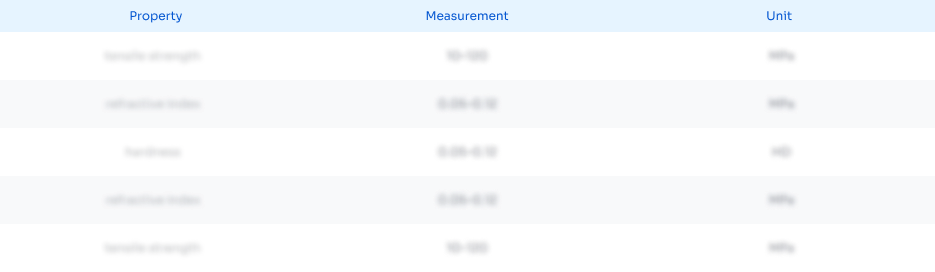
Abstract
Description
Claims
Application Information

- R&D Engineer
- R&D Manager
- IP Professional
- Industry Leading Data Capabilities
- Powerful AI technology
- Patent DNA Extraction
Browse by: Latest US Patents, China's latest patents, Technical Efficacy Thesaurus, Application Domain, Technology Topic, Popular Technical Reports.
© 2024 PatSnap. All rights reserved.Legal|Privacy policy|Modern Slavery Act Transparency Statement|Sitemap|About US| Contact US: help@patsnap.com