Metal, ceramic powder and polymer mixture used for manufacturing metal and ceramic products and method for hydrolyzing and removing polymer from moldings
A technology of powder and ceramics, which is applied in the fields of ceramic powder mixtures, polymer materials and metals. It can solve the problems of environmental hazards, waste of resources, and waste, and achieve the effects of low removal temperature, short time, and reduced product costs.
- Summary
- Abstract
- Description
- Claims
- Application Information
AI Technical Summary
Problems solved by technology
Method used
Examples
Embodiment 1
[0025] Create iron-based items. The material material is a mixture of carbonyl iron powder and hydrolytic decomposition of the main polymer material system. The carbonyl iron powder with a volume ratio of 59%, the combined volume of the polymer material system is 41% (of which: 90% caprolactam, 7% low-density polyethylene, 3% polyisobutylamine). First, the carbonyl iron powder with a volume ratio of 59% of the mixture, low-density polyethylene with a mass ratio of 7% in the polymer material system, and 3% polyisobutylamine are pre-mixed in a mixer for 1 hour, and then mixed in a kneader. Knead at 130°C for 1 hour; then evenly put caprolactam with a combined mass ratio of 90% in the polymer material system, knead at 100°C for 1 hour, transfer the material to an internal mixer and knead at 110°C for 0.5 hours to obtain a blend; then Transfer the mixture into the extruder, extrude, dry, and granulate; the green product is obtained by injection molding with the injection machine;...
Embodiment 2
[0027] Manufacture of stainless steel products. Material material 316L stainless steel powder and hydrolytic decomposition of the main polymer material system combination mixture. 316L stainless steel powder with a volume ratio of 63%, the combined volume of the polymer material system accounts for 37% (of which: 92% polybutylene terephthalate, 5% polypropylene, and 3% polyisobutylene); 316L stainless steel powder with a volume ratio of 63%, and a polymer material system with a mass ratio of 5% polypropylene and 3% polyisobutylene, pre-mixed in a mixer for 1 hour, kneaded in a kneader at 220 ° C for 1 hour; Put it into the polymer material system and combine the mass ratio of 92% polybutylene terephthalate, knead at 180°C for 1 hour, transfer the material to an internal mixer and knead at 185°C for 1 hour to obtain a blend; The mixture is transferred to the extruder, extruded, dried, and granulated; the green product is obtained by injection molding of the injection machine; ...
Embodiment 3
[0029] Manufacture ceramic products. The material material is a mixture of alumina powder and a polymer material system that has been hydrolyzed to remove the main components. Alumina powder with a volume ratio of 58%, the combined volume of the polymer material system accounts for 42% (of which: 2-pyrrolidone with a mass ratio of 89%, 8% low-density polyethylene, 3% polyisobutylene, and 58% of the material Materials Alumina powder, 8% low-density polyethylene and 3% polyisobutylene are pre-mixed in a mixer for 1 hour, put into a kneader and kneaded at 220°C for 1 hour; The polymer material system combines 2-pyrrolidone with a mass ratio of 89%, kneads at room temperature for 1 hour, and transfers the material to an internal mixer for 0.5 hours at 85°C to obtain a blend; then transfer the blend to an extruder , extruded, granulated, and dried; the green product was obtained by injection molding with an injection machine; the green product was put into a hydrolysis removal fur...
PUM
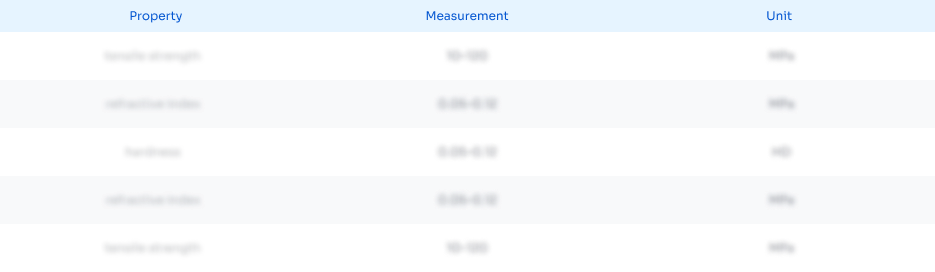
Abstract
Description
Claims
Application Information

- R&D
- Intellectual Property
- Life Sciences
- Materials
- Tech Scout
- Unparalleled Data Quality
- Higher Quality Content
- 60% Fewer Hallucinations
Browse by: Latest US Patents, China's latest patents, Technical Efficacy Thesaurus, Application Domain, Technology Topic, Popular Technical Reports.
© 2025 PatSnap. All rights reserved.Legal|Privacy policy|Modern Slavery Act Transparency Statement|Sitemap|About US| Contact US: help@patsnap.com