A manufacturing process of fir-tree-shaped blade-root type steam turbine blade
A steam turbine blade and manufacturing process technology, which is applied in the directions of manufacturing tools, metal processing equipment, metal processing machinery parts, etc., can solve the problems of high manufacturing cost of large blades, low blade qualification rate, etc., to ensure effective processing and forming, and improve the qualification rate. , the effect of controlling the position error
- Summary
- Abstract
- Description
- Claims
- Application Information
AI Technical Summary
Problems solved by technology
Method used
Image
Examples
Embodiment Construction
[0032] All features disclosed in this specification, or steps in all methods or processes disclosed, may be combined in any manner, except for mutually exclusive features and / or steps.
[0033] The main technological route steps of this technical scheme are as follows:
[0034] A, rough incoming material.
[0035] B, Milling blade root and blade crown clamping process head.
[0036] C, Rough milling of all parts except the blade root. Utilize the positioning of the three pinholes, and use the integrated processing method to roughly process the profile of the steam channel and the crown of the blade.
[0037] D, fine milling of all parts except the blade root and process benchmark. Utilize the positioning of the three pinholes, and in the way of integrated processing, finish machining the blade steam channel profile, tie bars, blade root intermediate, blade crown and blade crown process benchmark.
[0038] E, Rough milling blade root profile. The blade root intermediate an...
PUM
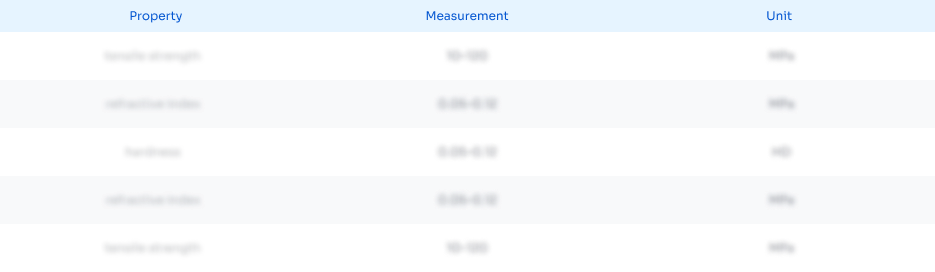
Abstract
Description
Claims
Application Information

- R&D
- Intellectual Property
- Life Sciences
- Materials
- Tech Scout
- Unparalleled Data Quality
- Higher Quality Content
- 60% Fewer Hallucinations
Browse by: Latest US Patents, China's latest patents, Technical Efficacy Thesaurus, Application Domain, Technology Topic, Popular Technical Reports.
© 2025 PatSnap. All rights reserved.Legal|Privacy policy|Modern Slavery Act Transparency Statement|Sitemap|About US| Contact US: help@patsnap.com